A More Sustainable Future with Continental
Sustainability is deeply embedded in our core values and our corporate strategy. Why? Because sustainable and responsible business practices enhance our ability to innovate and reinforce our viability for the future. We firmly believe that sustainable business is the only path forward. On this journey toward a more sustainable future, sustainable solutions are crucial for lasting success. But these innovations should not just stay in the showroom; they belong on the road. As a global technology company, we are committed to transforming our ideas into tangible products as swiftly as possible. This is where Continental excels. Drawing on over 150 years of production expertise and a deep culture of innovation, we embrace our responsibility to drive progress and help shape a more sustainable tomorrow. Year after year, we develop innovative technologies that set new standards, while continuously improving our existing products and processes.
A More Sustainable Future with Continental
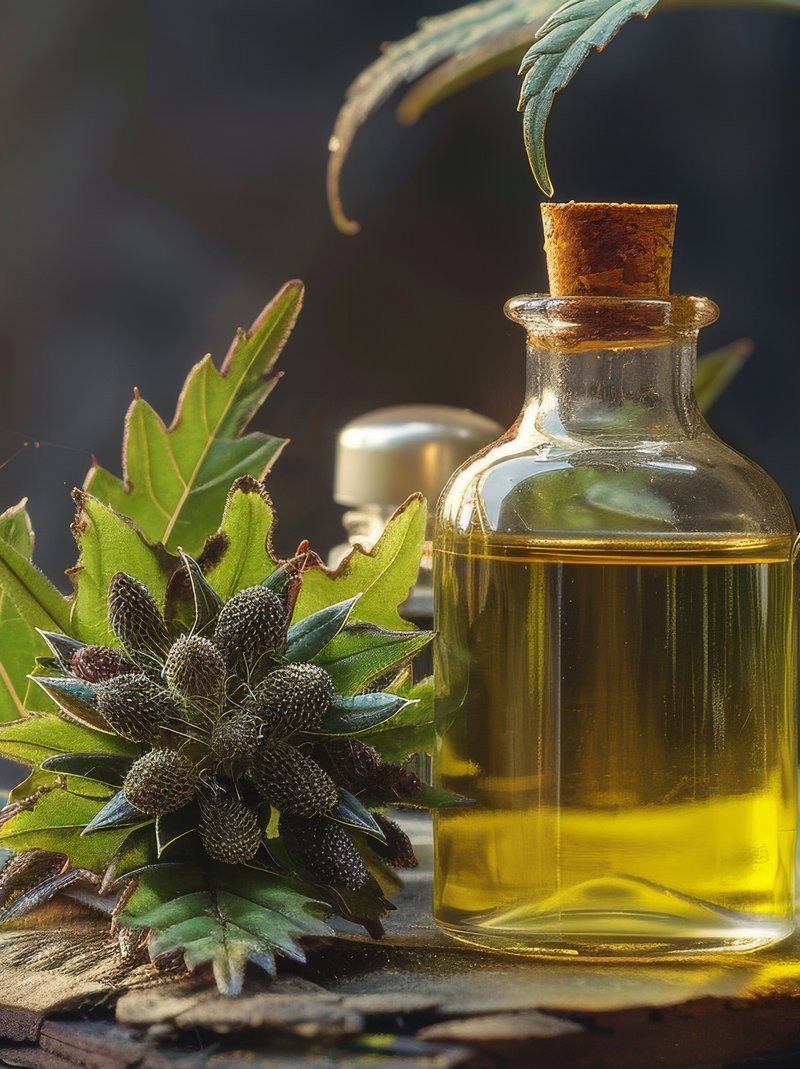
Sustainability is deeply embedded in our core values and our corporate strategy. Why? Because sustainable and responsible business practices enhance our ability to innovate and reinforce our viability for the future. We firmly believe that sustainable business is the only path forward. On this journey toward a more sustainable future, sustainable solutions are crucial for lasting success. But these innovations should not just stay in the showroom; they belong on the road. As a global technology company, we are committed to transforming our ideas into tangible products as swiftly as possible. This is where Continental excels. Drawing on over 150 years of production expertise and a deep culture of innovation, we embrace our responsibility to drive progress and help shape a more sustainable tomorrow. Year after year, we develop innovative technologies that set new standards, while continuously improving our existing products and processes. Below are some of our latest highlights:
On the Path to Generating Emission-Free Energy
We are combating climate change – for example, by developing products that help reduce carbon emissions. But it is not just the products themselves that contribute to greater sustainability; it is also the way we do things – how we bring these innovations into the world. For us, sustainable production and energy-efficient plants are crucial to a successful future. This is also reflected in our strategy: we aim to achieve carbon-neutral production globally by 2040 at the latest.
We are in the process of developing our production facilities into more sustainable factories focused on energy and resource efficiency with low emissions. Since 2020, all the electricity purchased for all our plants worldwide has come from renewable energy sources. We have taken important steps at a variety of locations. In 2023, our Tires group sector achieved a total of 26.2 megawatts of peak capacity from its new photovoltaic installations, enabling Continental to generate up to 27.9 gigawatt hours of additional green electricity each year. That is equivalent to the annual consumption of around 2,300 average German households. The facilities at our tire plants in Hefei (China), Rayong (Thailand), Hanover (Germany), Korbach (Germany) and Lousado (Portugal) were expanded. And a new installation was built in Alor Setar (Malaysia) as well.
Our ContiTech group sector is also prioritizing photovoltaics at several locations, including Timișoara (Romania), Subotica (Serbia), Szeged (Hungary), Wagrowiec (Poland), Weißbach (Germany), Changzhou (China), Kalayani (India) and Chihuahua (Mexico). Together, these facilities will now generate as much electricity annually as is consumed by the equivalent of around 3,000 households in Germany. To accelerate this shift to green energy, we have also initiated three pilot projects for sustainable production in Changzhou, Granby (Canada) and Dannenberg (Germany). These plants will serve as a guide to other locations on how to implement similar measures and as role models for other sites.
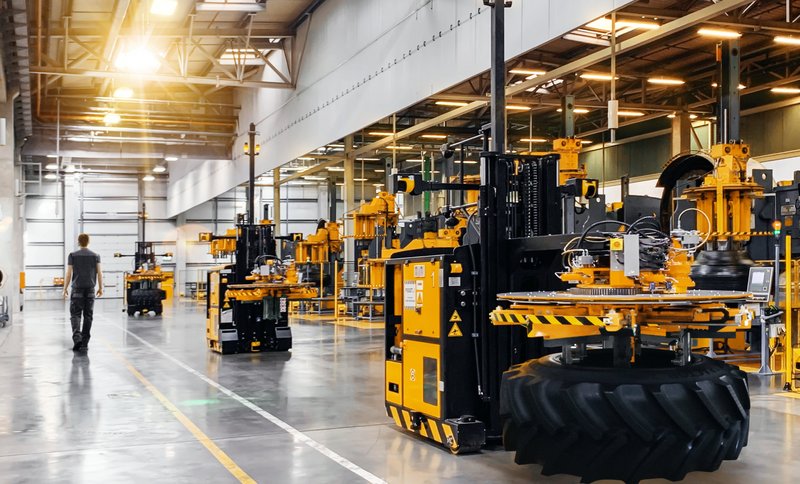
Another such role model is our tire production facility in Lousado, northern Portugal, which has enabled carbon-neutral production since the beginning of this year. This is thanks to a fully electric steam boiler that runs on solar power generated by us at the plant and on green energy from the electricity grid. The boiler generates steam for vulcanization, a key process in converting raw rubber into a flexible, elastic form using thermal energy. The potential of this technology is huge. Continental’s Lousado plant has a production capacity of more than 18 million tires per year. One of the tires manufactured there is the UltraContact NXT, our most sustainable production tire to date.
Our goal is to manufacture our products from 100% sustainable materials by 2050 at the latest. And we are now one step closer to achieving this: our four tire plants in Hefei (China), Lousado (Portugal), Púchov (Slovakia) and Korbach (Germany) have been awarded the International Sustainability and Carbon Certification (ISCC) PLUS, joining the two German ContiTech locations in Waltershausen and Eislingen. Further plants are soon to follow.
Shaping the Technologies of Tomorrow with More Sustainable Materials
At Continental, we focus on critical questions: how can we act more sustainably, ensure responsible sourcing and do more for the climate? And we are finding answers – for example, when it comes to increasing the share of sustainable materials in our products. We define as sustainable all materials that come from a closed material cycle, have no harmful effects on people or the environment, are sourced responsibly and are carbon-neutral along the entire supply chain. Our expertise and experience help us determine what makes economic sense in order to continuously improve the carbon footprint of our innovations. Because, as is so often the case, it is the mix that counts.
And it is precisely this mix that our ContiTech materials experts have refined in two products. First, in air springs for commercial vehicles, we have largely replaced synthetic rubber with a mixture of natural rubber and ethylene-propylene-diene-monomer (EPDM) rubber. This new rubber compound is resistant to both cold and heat, thus slowing down material aging and reducing other harmful environmental influences. This makes it suitable for a broader range of high-performance applications, while it retains its dynamic properties. The carbon footprint of the rubber compound has been reduced by more than 50 percent compared with conventional air springs.
Second, our Conti NXT V-ribbed belt for the aftermarket business is a true pioneering achievement from our materials experts. Compared with conventional V-ribbed belts, almost two-thirds of the Conti NXT is made from sustainable materials, including recycled PET bottles, organic fibers and recycled carbon black.
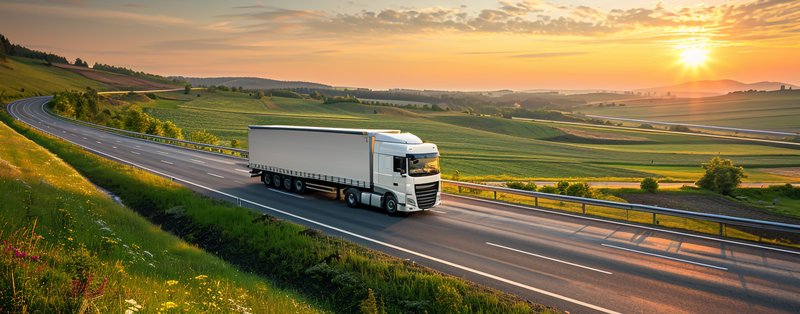
In fact, the use of sustainable materials has been steadily increasing across all our business areas for some time now. Our tires are also becoming more and more sustainable. Take, for example, our Conti Urban NXT, Continental’s most sustainable commercial vehicle tire yet. It is ideal for delivery vehicles and electric buses in towns and cities – and contains 59 percent renewable, recycled and ISSC PLUS mass balance-certified materials. The mass-balance approach mixes bio-based and circular materials with conventional materials within the same production system, and tracks the respective certified quantities along the entire production chain. This ensures full transparency and material traceability within the product. The rolling resistance of the Conti Urban NXT has been reduced by 25 percent compared with its predecessor, the Conti Urban HA3. This means lower carbon emissions for vehicles with combustion engines and up to 15 percent greater range for electric vehicles. High-density interlocking sipes ensure a secure grip, superior tracking and excellent braking performance – also in wet conditions and throughout the entire service life of the tire. The specially developed rubber compound reduces tire abrasion and enhances resistance to cuts, cracks, chips and breakage. The mileage of the Conti Urban NXT is also around 15 percent higher than its predecessor. Boasting extremely low external rolling noise, the Conti Urban NXT is an EU taxonomy-eligible tire, making it well suited to the requirements of electric-vehicle fleets.
New Tires Made from Recycled Carbon Black
For us, a world without waste is not a pipe dream. We are already working on achieving a circular economy together with all our partners along the value chain by no later than 2050. Our aim is to effectively reuse products, components and materials after their use phase.
Tires, for example, are made of a variety of materials and must meet the highest safety standards. Turning old tires into new ones is therefore a challenge, unlike plastics, glass, paper and many metals. While components like steel, and even the tread, can already be separated mechanically, rubber compounds are trickier and need to be separated chemically too. Through pyrolysis, rubber compounds are broken down into some of their base materials – mainly oil, gas and carbon. Pyrolysis oil can be used to produce new raw materials, for example. To further improve tire recycling through pyrolysis, Continental is collaborating with Pyrum Innovations and other recyclers. Pyrum breaks down our used tires into their individual components in industrial ovens using a special pyrolysis process. This process extracts valuable raw materials from the used tires, which can then be recycled. Recycled carbon black is used in all forklift tires manufactured at the Continental tire plant in Korbach, Germany. The next step is to use it in car tires as well.
Today, a standard car tire from Continental is already made from around 15 to 20 percent renewable and recycled materials. Our ambition is to use more than 40 percent renewable and recycled materials in our tires by 2030. In the long term, the use of recycled carbon black will bring us closer to this goal.
Carbon black is not only an important raw material for tire production; it is also used in the manufacture of other industrial rubber products. Our ContiTech group sector, for example, uses this recycled raw material to manufacture sustainable belts and other products. The targeted use of carbon black in rubber compounds increases the stability, strength and durability of our products. In its recovered form, it also helps mitigate climate change, since we require fewer fossil fuels and are able to reduce carbon emissions. This will bring us another step closer to our ambition of a circular value chain by 2050 at the latest.
“With 'Design for Recycling', we start by consequently thinking about the end – and beyond.”
We encounter the topics of sustainability and resource conservation in almost every area of life. How are these expressed in the field of vehicle interior surfaces? An interview with our experts Christoph Seeger and Manfred Jahncke about current developments and the future of interior surfaces.
Click here for the complete interview.
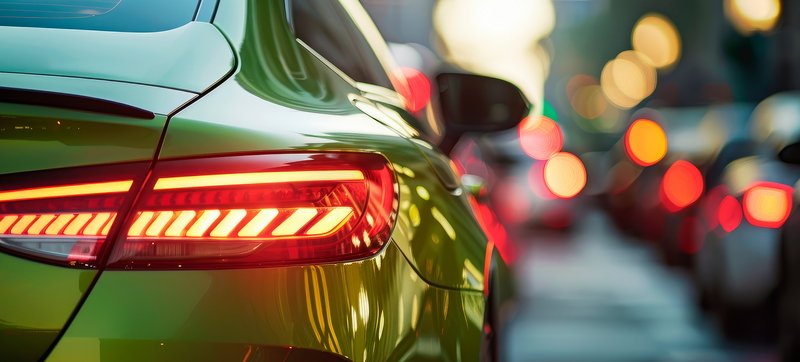
Next-Generation Brake Fluid Makes a Difference
When developing sustainable products, we focus not only on original equipment but also on the replacement business – for instance, workshops. Sometimes, it is the seemingly small things that really make a difference. Take brake fluid, for example. Not just any brake fluid – but a completely new generation. That is exactly what we have developed for our ATE New Original product line.
The ATE SecuBrake brake fluid from our Automotive group sector combines sustainability with occupational safety. It is produced using renewable raw materials and is free from hazardous substances that require regulatory labeling. This improves the carbon footprint and simplifies handling in the workshops, since there are no legally required safety measures for using or storing it. ATE SecuBrake is less harmful to health since it is completely free of borate esters, a chemical compound commonly used in DOT-4 brake fluids to enhance temperature and moisture resistance. ATE SecuBrake fully complies with these requirements without the need for any borate esters.
ATE SecuBrake is suitable for all drive types, including electric vehicles. The brake fluid is entirely manufactured in Germany, including its packaging. The ensures shorter transport routes, boosting sustainability. Sometimes, it is the seemingly small things that really make a difference.
Step by Step to a Circular Economy
As demand for more sustainable products grows, so does our commitment to achieving a circular economy within our value chain by 2050 at the latest. But how can we transition to sustainable production without a complete overhaul or temporary shutdown of machinery? One answer is mass balancing – a smart method that makes sustainability a reality one step at a time.
Mass-balanced products are based on a sophisticated system: they are no longer made solely with conventional materials. Their production also incorporates certified bio-based and recycled materials. Even though these two types of raw materials are mixed together, we document their proportions meticulously, so that we can trace them throughout the entire production chain. This allows us to precisely allocate the quantity of sustainable materials to the final product. With this approach, we can integrate alternative materials into production without completely overhauling existing processes.
The growing adoption of this innovative method has also been recognized by others. For example, our ContiTech sites in Waltershausen and Eislingen were recently awarded the prestigious International Sustainability and Carbon Certification (ISCC) PLUS. Prior to this, our tire plants in Hefei (China), Lousado (Portugal), Púchov (Slovakia) and Korbach (Germany) had already received this certification. This recognition marks another important milestone for us on our journey to a sustainable future. Step by step, we are increasing the share of renewable and recycled raw materials in our products and are able to trace them. This enables us to help our industrial customers worldwide to achieve their sustainability goals and drive forward the transition to a circular economy.
Better Every Year: What Others Are Saying About Continental
Sustainability is deeply embedded in our corporate strategy. Through our business, products and services, we are driving the ongoing transformation of the economy toward a healthy ecosystem for sustainable mobility and industries. The facts speak for themselves – and we can see the progress. But it is even more rewarding when others recognize these efforts. When our hard work is acknowledged globally through top ratings and awards, it proves that we at Continental are on the right track.
One example is the EcoVadis sustainability ranking in which we have been participating continuously for several years. This globally recognized assessment system evaluates the quality of companies’ sustainability management. In the 2024 fiscal year, Continental received the gold medal in this ranking. An achievement we are extremely proud of.
Top marks for climate change mitigation
Another milestone is the recognition from the international non-profit organization CDP. For 2024, Continental once again achieved an excellent rating, confirming its commitment to climate change mitigation and sustainability: an “A-” in the area of climate change mitigation and a “B” in the category of water security.
For us, a world without waste is not a pipe dream.
And we were finalists for the 2024 German Sustainability Award in two categories: as a company in the “Plastics and Rubber Industry” category and with our skai VyP Coffee upholstery covering in the “Resources” transformation field. This innovative product from our ContiTech group sector is made using recycled coffee grounds, meaning it is highly resource-efficient.
We are also proud to be reconfirmed a key member of the sustainability-focused FTSE4Good Index Series, which only includes companies with proven strong performance in environmental protection, social responsibility and corporate governance.
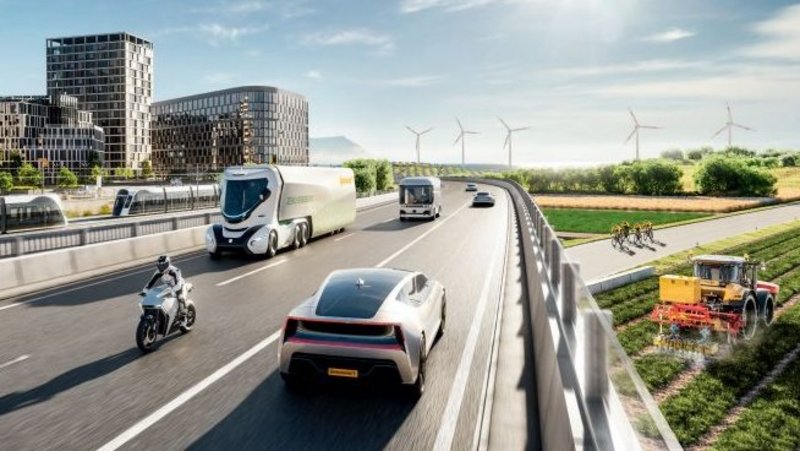
Please find here our Sustainability Report 2023 for our stakeholders in which we describe the values and principles we act on and how we measure our sustainability performance.
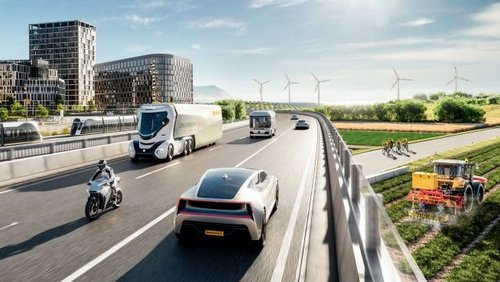