The Contidrom turns 50 – tire test facility more important than ever for Continental
- Since 1967 Continental has tested some 1.3 million tires at the Contidrom
- Systematic expansion from high-speed oval to high-tech test center
- All-weather AIBA automated test facility operational for five years now
The Contidrom, Continental’s “prototype” and benchmark tire test facility, is about to celebrate its 50th anniversary. Initially, the Contidrom comprised a high-speed 2.8-kilometer oval, which remains an impressive feature to this day. The other tracks, such as the 1.8-kilometer wet-handling course and the 3.8-kilometer dry-handling track were added during later expansion stages. Since 2012, important tests can also be conducted indoors in the all-weather Automated Indoor Braking Analyzer (AIBA). In all, Continental has tested some 1.3 million tires here since the facility first opened. The company’s future plans include an additional wet-handling course, which is to be an identical replica of the existing one. The idea is not to test even more tires, but simply to ease the pressure on this heavily used track. The Contidrom currently provides work for around 100 employees. With its wealth of precision testing options, the test track just outside Hanover has become more and more important over the years, driving progress in tire development in conjunction with the company’s R&D activities by documenting the performance characteristics of the tires out on the track. All of which help Continental to make an important contribution to greater road safety.
The latest addition to the test facilities is the AIBA, which was opened in 2012. In this all-weather test facility up to 100,000 braking tests a year can be conducted on dry, wet, and even icy road surfaces. Aided by the extremely precise findings delivered by the AIBA, Continental has been able to make further progress in the development of passenger car, van and 4x4 summer and winter tires. The facility is housed in a hall 300 m long and up to 30 m wide. Inside the hall, a driverless test vehicle is accelerated to speeds of up to 115 km/h fully automatically and then braked to a standstill by a braking robot on various standardized road surfaces that can be exchanged with the aid of hydraulics.
From the outset, the test engineers at the Contidrom have defined standards that are applied in Continental’s tire testing activities around the world, enabling findings to be uniformly interpreted and communicated within the company. Over the years they have repeatedly come up with new and pioneering test procedures. Back in the mid-1970s for example, a driverless Type /8 Mercedes put in endless laps of the oval while completing a variety of tests. Like today, however, these automated tests were no replacement for the personal impressions of a test driver. Many tests, including handling on the ragged edge, wet handling, steering properties and comfort, still call for the presence of a test driver at the wheel.
The original oval and the two handling tracks have since been joined by a number of other testing and measurement tracks. 1985 saw the advent of braking and aquaplaning tests on rail-guided tracks, while two circular tracks of different sizes serve primarily for tire tests in the wet. One circle is mainly used to simulate aquaplaning when cornering, while the other features different road surfaces that can be irrigated by sprinkler systems. In real-world driving both of these situations represent critical scenarios and therefore need particularly thorough testing during tire development. Another test conducted on a circular track delivers findings on the safety reserves of a tire with a slow puncture: A car or truck circles the track at 55 km/h. In the course of each lap, the pressure in the tires is reduced by 1/10 bar, until the tire literally rolls off the rim.
In 2003 an off-road section was opened at the Contidrom. With its various gradients, an axial twist track, a steep incline and a water basin, this is ideal for testing off-road tires on 4WD vehicles.
Making mobility more eco-friendly calls for tires with rolling resistance that is as low as possible, as well as low tire/road noise. Tire/road noise is measured and evaluated on two acoustics tracks located well away from the other courses. Both exterior and interior noise levels are recorded on a number of standardized surfaces. To make this possible, the vehicles’ engines, transmissions and powertrains are encapsulated in such a way that only the tire/road noise is measured.
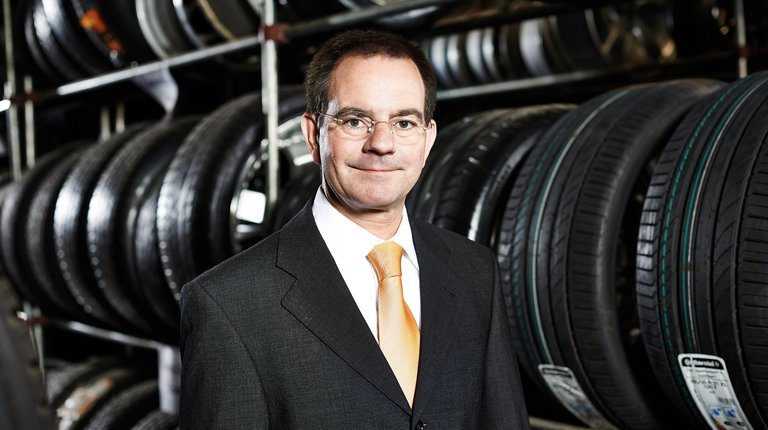
Klaus Engelhart
Press Spokesman
Passenger Car Tires / Germany, Austria, Switzerland
- +49 511 938-2455