Intelligent Drive Belts Enable Preventive Maintenance and Reduced Maintenance Outlay
- Sensor technology enables real-time status monitoring
- Continuous monitoring prevents downtime and costly repairs
Hanover, April 2017. Being able to replace components at just the right time, thereby avoiding extended periods of downtime? At the Hannover Messe 2017, ContiTech will be showcasing a range of concepts for intelligent drive systems and solutions demonstrating that this is no longer simply a vision for the future. Targeted monitoring is designed to enable preventive maintenance, which means that operators can respond to belt defects before they happen and replace the component accordingly.
“We envisage a future in which our intelligent belts can measure and monitor key belt states such as temperature, elongation, corrosion in the steel cord and surface wear – in accordance with the specific application requirements,” explains Svenja Lüker from the ContiTech Power Transmission Group’s innovation management team. Depending on its application and type, the belt is fitted with external and internal sensors that send the data directly to a PC or control unit. Preventive maintenance, which is carried out following analysis of the data, can be applied in both the automotive sector and in industry, for example on special machinery or hard-to-access drives. “We are investing in the development of different technologies so that we can create specific solutions for different applications in the future,” says Lüker. “The data generated will form the basis for furthering development in collaboration with our customers, thereby enabling us to create solutions that are tailored to specialist customer requirements and their specific application,” she continues.
Customers will benefit from preventive maintenance in two important ways. If the surface of a belt is cracked, for example, this can be detected early on by the sensor technology. Mechanics can then replace the belt before the crack leads to total failure or further, greater damage. Firstly, this prevents downtime and secondly, costly repairs. Operations become more efficient, too. “Thanks to this new approach, not only are we offering our customers holistic solutions, but we are also evolving from a simple product and system provider to a service provider,” says Philip Nelles, who heads the Power Transmission Group.
Visitors to the booth will even have the opportunity to test this brand-new technology for themselves. By pressing a button, they can allow hot air to flow through the cutout of a demonstration belt. The air heats up the belt, and the belt instantly outputs the corresponding temperature data on a monitor. The visitors can observe and monitor this process on the screen up close and in real time.
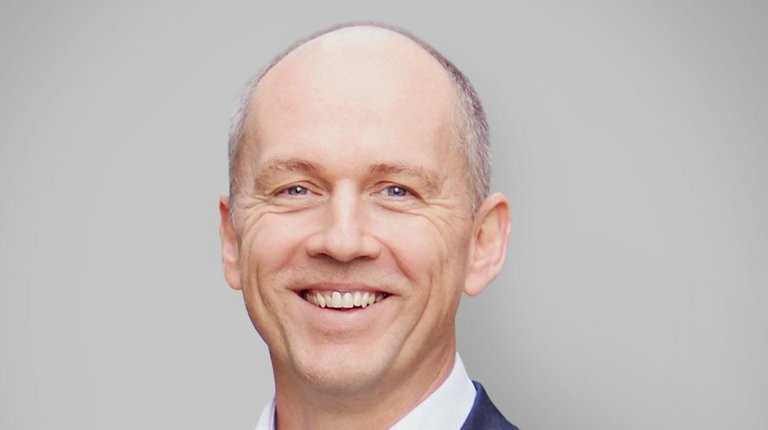
Wolfgang Reinert
Head of Media & Public Relations
ContiTech
- Insulation System with Multiple Potential Smart Applications
- Radar Sensor for Intelligent Solutions in Industrial Applications
- Intelligent Drive Belts Enable Preventive Maintenance and Reduced Maintenance Outlay
- ContiTech Presents Highly Accurate Measurement Technology and the Strongest Steel Cord Conveyor Belt in the World
- Conti Professional: New Functionalities Added to Drive Design Software
- ContiTech Further Develops App for Mobile Vibration Analysis
- Hannover Messe: ContiTech Rewards Reliable Partners