Closed-Trough Conveyor Belts Ensure Energy-Efficient and Low-Dust Coal Transport in China
- Closed-trough conveyor belts enable clean material transport through rough terrain at one of China’s largest coal mining sites
- Closed conveyor system with low rolling resistance saves 2,880 metric tons of coal dust emissions each year and protects the environment
Hanover, May 29, 2019. In Yangquan, northern China’s Shanxi province, Continental is using a closed-trough conveyor belt system to ensure the smooth and environmentally friendly extraction of pit coal. The closed system minimizes dust emissions at operator YanKan Coal’s mining site, and is also fireproof and has low rolling resistance, making it particularly energy-efficient. The system, which is one of the longest closed-trough conveyor belt systems in China, covers a distance of 8.1 kilometers.
Be it smartphones, tablets, gasoline and electric drives, buildings, machinery and vehicles, or even their production sites; they all have one thing in common: They all need energy and raw materials in order to be produced and operated. For this reason, oil and natural gas, precious metals, rare earths, iron ores as a raw material for steel processing and of course coal, are mined, collected and extracted around the globe. In China, coal serves as a major source for national energy production, making it the most important resource for covering the country’s vast energy requirements. The densely populated country has developed tremendous demand for energy due to rapid industrialization, its booming economy and the associated standard of living in recent decades. And there is plenty of coal in China; in particular, the autonomous Inner Mongolia and Shanxi regions in the north of the country have large deposits of the fossil fuel. The People’s Republic currently covers about 60 percent of total energy production by mining it (source: Reuters)*. This makes the People’s Republic one of the largest producing countries in the world.
Making coal mining environmentally friendly while at the same time investing in the expansion of renewable energies are important aspects of China’s energy policy. This is where the products from Continental help.
Clean material transport for better air and added safety
In China, as is the case around the globe, it is all about balancing the energy needs of the population and industry on the one hand, with climate change mitigation on the other. “For the operators of mining facilities, the fundamental question is which technical solution is the safest, most reliable and cost-effective method of transporting coal and other raw materials from the perspective of climate protection and energy efficiency,” says Stephan Weisgerber from Continental in China.
The operator of the coal mine, YanKan Coal, in the northern Chinese province of Shanxi, is therefore relying on Continental closed-trough conveyor belts, also known as pipe conveyor belt. Especially with the demand of the Chinese government for climate protection in coal mining, these are increasingly becoming the means of choice. In general, conveyor belts have emerged as the financially and environmentally more advantageous transport solution within a certain distance compared with alternatives such as truck fleets, since their operation emits less CO2 and there is no need for empty trips. Closed systems such as tube conveyors also offer other decisive benefits. They minimize dust emissions. In addition, the transported material itself is well protected against environmental influences such as wind, snow, sun and rain. “This is done by rolling up the belt,” explains Weisgerber. The outside edges of the belt overlap throughout the entire duration of transportation like a protective casing for the transported material. Only when taking up and delivering material do the closed-trough belts open up and assume the shape of a conventional conveyor belt.
It is estimated that coal dust emissions caused by gusts of wind, snow and rain amount to 0.12 percent of transported materials when open conveyor systems are used. In Yangquan, the Continental tube conveyor, with a width of 1,600 mm and an outer pipe diameter of 458 mm, transports 1,000 metric tons of coal per hour and 2.4 million metric tons of coal per year. “This results in an enormous saving of 2,880 metric tons of coal dust emissions per year – and thus significantly improves air quality. Thus, our system also protects the health of mine workers and improves the quality of life of the people living in the area,” Weisgerber emphasizes.
“We decided to use Continental’s closed-trough conveyor belts because they fully meet the relevant requirements with regard to climate protection, safety and efficiency,” says BiGui Chen from YanKan Coal. Continental’s technology helps meet stringent safety regulations for coal mines that dictate the maximum concentration of dust in the air. This is required not only when it comes to health and air quality, because among the most dreaded accidents in mining are coal dust explosions – a destructive reaction of coal dust with oxygen. These can occur very quickly when whirled particles of coal dust react with the oxygen in the air due to sparks, heated parts of equipment or similar. “The closed system from Continental is ideal, because no dust can escape. The closed-trough conveyor belts in Yangquan are also flame-retardant, adding another layer of safety,” BiGui Chen adds.
Flexible adaptation artist for rough terrain
Shanxi’s coalfields account for 37 percent of the province’s total area. There are approximately 200 billion metric tons here, which roughly equates to one third of China’s coal deposits (source: China Tourism)**. Much of the province is more than 1,000 meters above sea level. Consequently, the 13.37-square-kilometer mining area of YanKan Coal Ltd. in Yangquan, which is equivalent to approximately 1,870 football fields in size, is also hilly and almost impassable.
In mining, whether above or below ground as well as in industrial applications, large inclines and tight bends with low space requirements and high mass flows must often be overcome. While the angle of incline of troughed belt conveyors is usually 20° or less and curve radii remain very large, a pipe conveyor allows curve radii and tilt angles of up to 30°. The Yangquan closed-trough conveyor belt overcomes elevation differences of up to 172 meters over its 8.1-kilometer stretch from the coal deposit to the transfer station, going through a complex route with over 39 convex, concave and 20 horizontal bends. “Our closed-trough conveyor belt easily masters tight bends and steep conveyor angles and thus adapts perfectly to the landscape to save space. Our system is characterized by the fact that it manages without transfer points,” says Ming-Ya Tang from Continental. This also has a positive effect on the installation costs of the assembly, which are generally cheaper than for assemblies with transfer points.
Quickly switching to energy-saving mode
In Yangquan, the closed-trough conveyor belt system transports pit coal at a high speed of 4 m/s or 14.4 kilometers per hour. This is about three times the speed of a pedestrian walking briskly or a cyclist riding at a moderate pace. In terms of efficiency, the system scores points not only with its speed, but also with its energy efficiency. Miles of conveyor belts can consume as much electricity as a small town. Continental has developed a solution for this, too. Using a special rubber compound has enabled it to minimize the rolling resistance of conveyor belts and thus significantly reduce their energy consumption. This arises when the belt runs over the idlers, and accounts for two thirds and therefore the largest share of the total resistive forces of a conveyor system. “With the right compound, we reduced the energy consumption involved in transporting raw materials by 25 percent. This special compound is also used in the facility in Yangquan. This will improve the facility's carbon footprint and save on energy costs for the operator,” says Weisgerber.
Measurements by the Institute for Transport and Automation Technology of the University of Hanover have confirmed results according to which a conveyor system five kilometers in length can save over 3,000 kW of energy. The energy saved in 1.5 hours is therefore as large as the average annual consumption of a household in Germany or that of five households in China.
The right solution for every application
In cooperation with conveyor manufacturer Sichuan Zigong Conveying Machine Group (ZGCMC) and the Continental experts in China, it has been possible to develop a closed-trough conveyor belt system in Yangquan that meets the highest conveyor system engineering requirements and optimally overcomes geographical hurdles – to the customer’s great satisfaction and ensuring the best possible protection for the climate and employees. Closed-trough conveyor belt systems such as the one in Yangquan are also unique. That is because every belt is custom-made to suit the local circumstances. Depending on the requirements, the closed-trough belt is designed with high-quality fabric or steel cable tension members.
One particular challenge is the precise transverse rigidity, which ensures a good tube shape so that the belt does not collapse. If the rigidity is too high, the belt moving resistance will be too high and energy consumption will rise. Here, the expert knowledge of the appropriate engineers is required. In addition, Continental’s customer service engineers in Shandong visit the coal mine on a regular basis to ensure smooth belting, measure wear and check the condition of the closed-trough belt. They remain in constant contact with the operator in the process.
Continental closed-trough belt conveyors have already proven themselves in many places in China – in coal mines as well as in power plants and steel mills. Yangquan’s Shangshe coal mine has a 4.9-kilometer closed-trough conveyor belt system in operation. At the Anyang coal mine in Chenghe (Shaanxi province) and the Hongyuan coal mine in Puxian (Shanxi province), there are also four-pipe conveyors with a total conveying length of 8.7 km. Further projects are already being planned.
Every material – whether coal, cement, waste material, hot slag, wastewater sludge or foodstuffs such as sugar and grain – requires its own conveyor system engineering solution. In addition, there are different climatic zones and topographies that impose specific demands on the conveyor systems. In recycling and gravel operations, in wood processing as well as in power plants, mines, cement or steel mills, in production or chemical plants as well as in harbors, deserts, mountains or rainforests – with its conveyor belt technologies, Continental is on hand wherever raw materials and others goods are mined, processed and distributed.
How the closed-trough conveyor belt system works
The Continental closed-trough conveyor belt system is troughed at the loading point and can be filled like a conventional conveyor belt here. Once the material has been loaded, specially arranged finger rollers ensure that the conveyor belt forms a closed circular belt. Further hexagonal idler stations along the conveyor route ensure closed guidance of the belt. As a result, the conveyed material is continuously protected by the closed belt system. At the end of the belting, the closed belt is opened by the arrangement of the idlers and takes on a flat shape on the pulley in order to unload the conveyed material just like on conventional belt conveyor systems.
*Source: https://www.reuters.com/article/us-china-energy/chinas-2018-coal-usage-rises-1-percent-but-share-of-energy-mix-falls-idUSKCN1QH0C4
** Source: https://www.china-tourism.de/provinzen/shanxi/
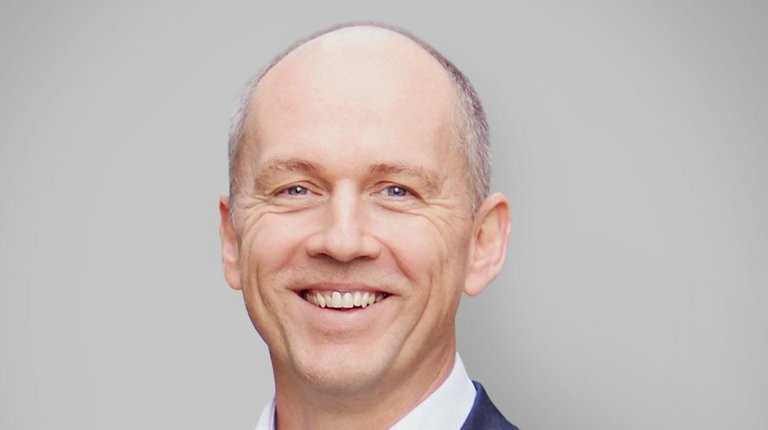
Wolfgang Reinert
Head of Media & Public Relations
ContiTech