Continental and Hanover University of Applied Sciences and Arts Collaborating on Efficient Intralogistics Processes
- Cooperation with the SCM (Supply Chain Management) Lab at Hanover University of Applied Sciences and Arts
- Material flows optimized to achieve efficient operating processes
- Virtual load scenarios simulated to ensure reliable processes in day-to-day operations
Langenhagen, September 30, 2019. Technology company Continental is collaborating with the SCM (Supply Chain Management) Lab of Hanover University of Applied Sciences and Arts with the aim of achieving ongoing optimization of order handling processes in the company’s Langenhagen-based European Distribution Center located. Up to 160,000 power transmission belts are shipped every day from the warehouse to European automotive aftermarket distributors. “Our goal is to achieve an optimum material flow in our intralogistics systems,” declares Ralf Zempel, project manager in the field of drive component logistics at Continental. “The scientific-based approach optimally complements our day-to-day operations. The students will benefit from the chance to conduct near-market research, while we will be able to share in their results in order to make our operations even more efficient and shorten delivery times.”
Continental completed the commissioning of the state-of-the-art distribution center in September after around one and a half years of construction work. The building complex has 34,000 square meters of floorspace, around 26,000 locations for pallets and a fully automated small-parts store. The company has invested more than ten million euros in the project. The warehouse has already been shipping surface materials for vehicle interiors to the automotive sector since the start of the year. The products for the automotive aftermarket, such as power transmission belts and kits (comprising one or more timing belts and other components), were then added in the summer.
Simulation of complex, highly dynamic processes
Continental is using the latest digital technologies in the distribution center. “We have a fully automated small-parts store, have installed a new warehouse management system and are using hand and finger scanners that are wirelessly integrated in gloves,” reports Zempel. “If you want to be competitive in today’s market, it’s important to have efficient processes – and these also reduce the staff workload.”
The Hanover University of Applied Sciences and Arts students have been following the commissioning of the new distribution center since the spring. The core questions for them included: How can the most effective order processing design be achieved? Where do critical areas occur? What happens if processes are changed? “Very complex, highly dynamic processes take place in the distribution center,” explains Prof. Christoph von Viebahn from the Business Information Systems department of Faculty IV – Business and Information Systems at Hanover University of Applied Sciences and Arts and adds: “We are able to run the various load scenarios virtually in simulations. Conducting digital trials like this before actual system implementation allows us to ensure that day-to-day operations can be handled smoothly, reliably and quickly.”
Potential for increasing efficiency
The university is also following operational processes in the distribution center and is in close contact with Continental in order to turn its research results into concrete measures. “We have already jointly developed a consolidation concept, i.e. merging the components from various sections of the warehouse,” reports Zempel. “In the future, we will process the individual components making up a consignment in parallel. This means locations will be occupied for shorter periods, the material flow rate will increase, and we will be improve overall performance.” The project manager also places particular emphasis within the logistical processes on the areas of picking, high-bay racking and tugger trains.
The collaborative partners plan to address more complex issues subsequently, such as the addition of further products and customers and continual process improvement – academia and industry operating hand in hand.
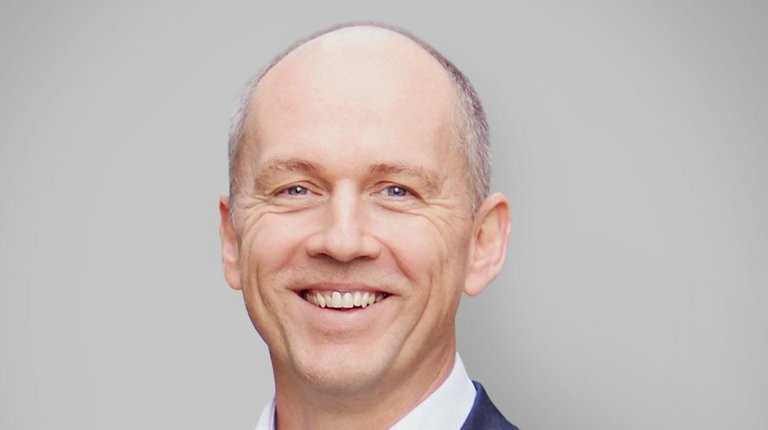
Wolfgang Reinert
Head of Media & Public Relations
ContiTech