The Ultimate High-Speed Rail Network: Continental Helps Connect China’s Megacities
- Continental’s air spring systems enable cutting-edge rapid-response vehicles to travel to maintenance sites for China’s high-speed rail network in record time
Hanover, August 2018. Technology company Continental has developed an air spring system that enables maintenance and response vehicles to travel rapidly between rail maintenance and construction sites. The system enables China to maintain, service and expand its high-speed rail network with maximum efficiency. Home to 1.4 billion citizens, the country is the largest in the world in terms of population, and the fourth largest based on geographical area. It also boasts the largest high-speed rail network. China has been focusing on rail travel as an environmentally friendly, reliable and high-performance transport option since the 1990s, and is expanding its network at an impressive pace. The China Railway High-Speed (CRH) development plan, launched in 2004, includes an ambitious objective of expanding the network from 19,000 to 30,000 kilometers by 2020. China is aiming to build four east-west and four north-south corridors capable of accommodating trains running at between 250 and 350 km/h. This expansion will mean that 80 percent of all large cities are accessible by high-speed rail. In response to this development, cities and regions have snowballed into huge urban sprawls and megacities. The rail network is the backbone of the essential infrastructure for transporting goods and people between these metropolises. “Our air spring systems for service vehicles are a key component of safe and reliable mobility in China,” says Günther Sengeis, key account manager for air spring systems at Continental.
The highest speeds demand the highest levels of safety
From Kunming, a city of 6.8 million people, high-speed trains dart across five provinces at up to 350 km/h to reach Shanghai – 2,264 kilometers away – in just under eleven hours. The world’s longest stretch of high-speed rail has reduced the journey time by 23 hours. In Europe, a similar journey by train – from Cologne to Moscow – would take 31 hours.
But there’s more to the CRH project than meets the eye. As well as expansion, the entire network and its overhead wiring need to be serviced and maintained to ensure that China’s high-speed trains are capable of transporting people and goods quickly, safely and efficiently. This is where Continental’s air spring systems for cutting-edge service and response vehicles come into play, helping to meet the incredibly demanding quality, reliability, operating safety and availability standards for overhead wiring on high-speed rail lines. “At the end of 2014, we delivered our systems for rapid-response service vehicles deployed in the Chinese high-speed rail network,” explains Sengeis. The vehicles can be used universally across the network. With applications ranging from servicing and maintenance to inspection, safety checks and troubleshooting and the replacement and construction of overhead wiring, they cover the entire spectrum of work involved in building and maintaining a rail network.
When every minute counts, Continental is first on board
Primary springs manufactured by Continental have been in use in work vehicles for decades. For this project’s work trains in China, the company has also developed and supplied a complete air spring system to enable the vehicles to travel swiftly between locations. “Our air spring system features secondary suspension between the bogie and the main frame, which enables the vehicle to travel safely and independently to its next service location at speeds of up to 160 km/h. Sometimes, this can involve travel distances of up to 2,500 km. By speeding up the journey to the next service location, it is possible to complete maintenance on the high-speed network significantly more quickly. From a financial perspective, this is of enormous benefit to the customer,” explains Jörg Frohn, head of product development for air spring systems for rail transport applications at Continental.
Yet another advantage of the air spring system is that it absorbs vibrations and shocks, making any uneven sections of track barely perceptible inside the train and making high-speed trains more comfortable for passengers. On work vehicles, employees can make use of the on-train workshop during the journey, enabling them to prepare for the task ahead so that they can take action rapidly upon arrival. The faster the work can be completed, the sooner the track can be re-opened. “As time pressure rises, there is less and less time available for maintenance and servicing. Greater efficiency is key to getting things done. This makes the reliability of our components all the more important,” Sengeis emphasizes.
Climatic conditions place huge demands on materials
Due to the sheer scale of the country, China has 18 different climate zones and some areas of extreme climatic contrast. Long and persistently cold winters with average temperatures of -25°C – dropping down to -40°C on extremely cold days – and torrid heat of +40°C in the summer are typical for the north of the country, while the regions in the east and south-east have very hot, subtropical summers. These diverse climate conditions place the greatest demands on materials, which must work reliably and last as long as possible in all areas of the country. “This is also true of our primary springs and air spring systems, which ensure that journeys for response vehicles are safe and quiet all year round,” says Sengeis. These conditions are significantly more challenging than those in less demanding climates, such as Western Europe, and they have a major impact on the service life of each air spring. In extreme heat or cold, these components must function with complete reliability in challenging environments throughout the year. The vehicles are heavily utilized and travel vast distances, so it is essential that components be long-lasting and reliable. “Over decades of work in Europe, we’ve built up the expertise needed to develop systems with outstanding resistance to extreme temperatures, abrasion and the effects of ozone, UV and other media,” adds Frohn. “We work with our customers to expand our knowledge of local factors, such as climate conditions and routes, to develop the best possible solutions for each market.”
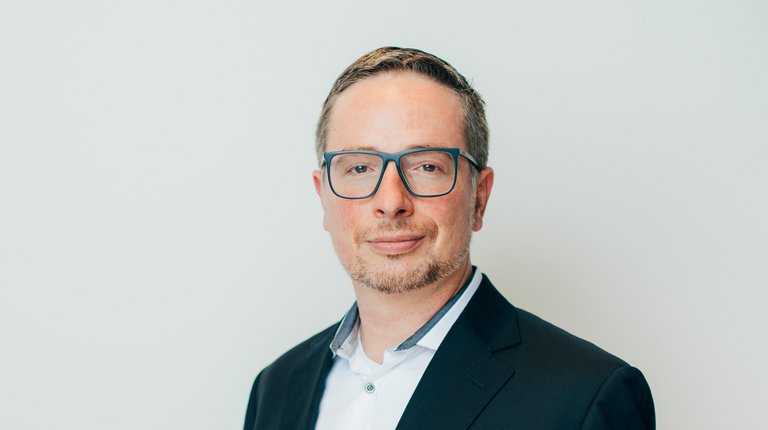
Sébastien Bonset
Media & PR Manager, Media Coordination APAC
ContiTech