Silica in Tires has Enabled Greater Safety and Sustainability on the Roads for Three Decades
- Continental replaced carbon black in tread compounds with silica for the first time in 1994
- Prof. Burkhard Wies, Head of Applied Research and Innovation for Continental Tires: "Silica in rubber compounds was a revolution in tire technology, enabling us to almost halve braking distances on wet road surfaces. This is still an enormous safety gain today"
- Rice husk ashes as an increasingly important base material for sustainable silica
Hanover, Germany, March 11, 2025. Thirty years ago, Continental used silica for the very first time in its tread compounds for car tires. The properties of this filler revolutionized the driving safety and energy efficiency of tires. Rolling resistance has been significantly reduced, and braking distances have since been cut by nearly 50 percent. This was made possible by the special surface properties of silica, which can form chemical bonds with the rubber polymer. During vulcanization – the process in which the tire obtains its shape – silica, as well as other components, is responsible for the formation of a very strong network between the rubber molecules. The result is an elastic tire with excellent safety properties. Today, silica has largely replaced carbon black in the tire tread and has become indispensable in many rubber compounds for car, van and two-wheeled vehicle tires. Its production is also becoming increasingly sustainable: Continental is already using a particularly sustainable silica that is obtained from rice husk ashes.
"Silica in rubber compounds was a revolution in tire technology, enabling us to almost halve braking distances on wet road surfaces. This is still an enormous safety gain today," says Prof. Burkhard Wies. In the mid-1990s, he worked on developing the first tires with silica in the rubber compound at Continental. He now heads the Applied Research and Innovation department. "Silica compounds are also good for the environment, as they reduce the rolling resistance of tires. This means less fuel consumption for combustion engines and increased range for today’s electric cars," explains Wies.
In the mid-1990s, the first production tires containing silica were launched on the market
Silica is used as a filler in many industries. In construction, for example, it is used in the production of concrete and bricks. Silica is primarily obtained from quartz sand. However, this crystalline silica is unsuitable for use in tire production. A technically prepared "amorphous" silica is used instead.
In the mid-1990s, Continental was one of the first tire manufacturers in the world to recognize the potential of silica as a filler for the tire industry. At the beginning of the decade, the Hanover-based company conducted the first very promising experiments. Its properties are activated during the mixing process, whereby the silica reacts with the binding agent silane. In the next step, the vulcanization process, the rubber mixture is then pressurized at temperatures of 120°C to 160°C. The tire obtains its characteristic appearance thanks to special tire molds. At the same time, sulfur is used to turn the rubber compound and silica into a flexible and elastic rubber. This is because the sulphur forms bridges between the long-chain molecular strands of the rubber during vulcanization. The silica – supported by silane – forms additional bonds between individual rubber polymers, creating a very strong network between the rubber molecules. This gives the tire physical properties such as outstanding wet grip, good abrasion resistance and excellent rolling resistance. At the same time, it can withstand extreme stresses.
The first road tests using the new filler in the tire compounds back in 1994 demonstrated huge improvements in braking on wet roads and rolling resistance compared with carbon black. A year later, Continental used silica for the very first time in a production tire, the ContiEcoContact CP. In 1996, this was followed by the launch of the ContiWinterContact TS 770, the first winter tire with silica in the tire rubber compound. "Together with the introduction of passive safety equipment such as seat belts and the anti-lock brake system, the use of silica in tires has helped to significantly reduce the number of road casualties," says Wies.
Greater sustainability with silica made from rice husk ashes
Continental’s developers are constantly working on making tires safer and more sustainable while delivering even greater performance. Both when it comes to the tire assembly and the materials used. For example, the company is researching the use of alternative, more sustainable silica with comparable properties and safety benefits. Rice husks have proven to be a reliable base material for sustainably manufactured silica. Rice husks are a by-product of rice production that cannot be used as food or animal feed. Manufacturing silica out of rice husk ashes is more energy-efficient than conventional materials such as quartz sand. Silica from rice husk ashes is already used in Continental’s most sustainable production tire to date – the UltraContact NXT.
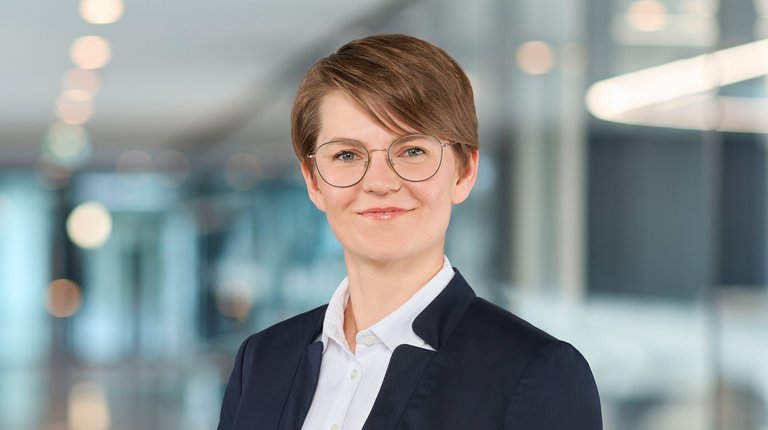
Katharina Bühmann
Communications Manager Technology, Innovation & Original Equipment Tires
Continental Tires
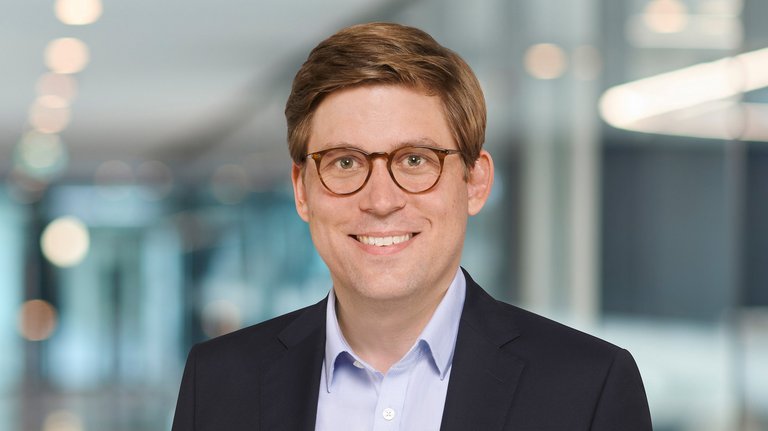
Henry Schniewind
Head of External Communications
Continental Tires