Continental’s New E-Motor Rotor Position Sensor: More Efficiency and Smoother Operations for Electric Vehicles
- Motor control with utmost efficiency: high-speed Rotor Position Sensor utilizes inductive technology to detect the rotor position in a synchronous electric machine
- Advantages over existing sensors of the resolver type are: It is highly efficient, lightweight, more compact and standardized for use across a wide range of motors
- Continental strives to become one of the leading electric motor position sensor suppliers in addition to its strong position in engine position sensors
Toulouse, France, February 22, 2023. Technology company Continental is expanding its sensor portfolio for the fast-growing electric car market with the unveiling of a new innovative sensor. The high-speed inductive e-motor Rotor Position Sensor (eRPS) detects the exact position of the rotor in a synchronous electric machine, which helps to increase efficiency and enables smoother operations. Compared to existing resolver sensors, the eRPS is more compact and 40 percent lighter in weight. Existing solutions for rotation measurement are often based on the resolver principle (a rotary electrical transformer), which is complicated and needs to be adapted to each type of synchronous motors specifically. The eRPS, however, is a standardized component for every motor regardless of the number of pole pairs. It is easy to carry over this new sensor from one motor to another, making it an attractive option for electric cars. The start of production is planned for the end of 2025.
“The growth in vehicle electrification translates into more synchronous motors in the car. This ranges from big and powerful ones like traction motors to smaller ones like electric pumps. Our standardized eRPS technology has a wide range of potential applications in electric vehicles,” said Laurent Fabre, head of the Passive Safety and Sensorics Segment at Continental. “Measurement precision, compact dimensions and the all-in-one sensor concept combining several functions add to a high level of integration in the car. Continental is one of the leaders in the supply of engine position sensors today. With the launch of the eRPS, we are now well positioned to be one of the leading suppliers for electric motor position sensors, too.”
Compactness and precision make the eRPS the ideal choice for electric mobility
The eRPS was specially developed to control synchronous motors (where the rotor rotates at the same speed as the revolving field in the machine). To achieve maximum motor efficiency, the motor control unit needs to know the exact position of the rotor, which makes this type of sensor an essential part of synchronous motor applications. While the resolver is a comparatively massive sensor, the eRPS is very flat and supports compact motor designs with a small overall length. The sensor design is based on eddy current principle and is optimized to increase robustness to mechanical tolerances. State-of-the-art integrated circuits (ICs) are used for signal processing. The IC has been designed according to ISO 26262 functional safety automotive standards to reach ASIL C. As an option, two ICs can be embedded in the eRPS to ensure the redundancy that is an integral part of functional safety.
Though the traction motor of an electric or hybrid vehicle is a prominent use case, there are many more synchronous motors in electrified vehicles. Future dry-brake systems (without hydraulics), for instance, will also be actuated electrically and will require rotation sensors. When developing the eRPS, Continental took on existing knowledge and experience with inductive technology. For example, the brake-by-wire system MK C2 uses an Inductive Motor Position Sensor and has been a benchmark for the sensing concept development with increased speed and accuracy, as is the case with the eRPS.
Precision motion detection via inductive technology
The new eRPS is an inductive rotor position sensor covering several integration configurations. The sensor can be mounted through the shaft, or it could be integrated at the end of the rotor shaft, including in this case the sealing function. The module contains excitation and reception coils embedding one or two ICs that detects directly the electrical angular position of the metallic encoder on the rotor shaft. This straightforward and weight efficient solution delivers an output in a format that requires minimal signal post processing. The electrical angular position data is required for an efficient e-machine torque control and to achieve the maximum service life of a motor.
“The signal pattern of the eRPS is much easier to work with than that of a resolver. The measurement principle is very fast, extremely robust and is suited for high motor speeds and acceleration. It is very compact and works with a minimal number of parts,” said Ronan LeRoy, head of Sensors and Subsystems Product Center in the Passive Safety and Sensorics Segment at Continental.
With a maximum current consumption of 15mA, the eRPS offers an electrical accuracy of ±0,5° for a four pole pairs motor. It is designed to cover rotational speed requirements needed for future electric vehicle platforms (~24.000 rpm). The sensor’s operating temperature range is very wide and falls within -40 °C to 140 °C and peaks up to 155 °C.
Comprehensive portfolio of sensors for the engine and battery of electric vehicles
The eRPS is extending Continental’s sensor portfolio specifically designed for electromobility to support both, road safety and electrification. With the Current Sensor Module and Battery Impact Detection, the company already introduced in the year 2022 two new solutions focusing on protecting the battery and/or on battery retention of electric vehicles.
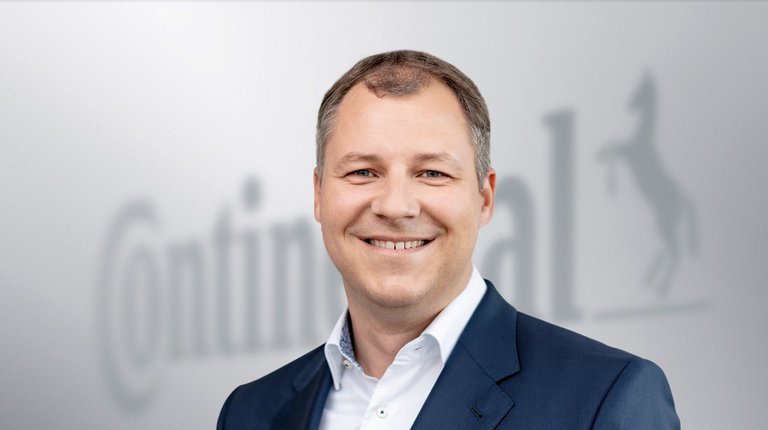
Sören Pinkow
Media Spokesperson Autonomous Mobility and Commercial Vehicles
Continental Automotive