ContiConnect 2.0: Updated Tire Pressure Monitoring System Convinces Haulage Firm G.Webb
- International Continental trial customer provides positive feedback on additions to the tried-and-tested tire pressure monitoring system
- Fewer punctures, better workshop planning and greater fleet efficiency
- Digital Solutions package is tailored to mixed-vehicle fleets and different operating times
Hanover, Germany, August 30, 2022. Haulage firm G.Webb based in Cambridgeshire, England is one of Continental’s international customers currently trialing the new platform for the ContiConnect tire pressure monitoring system. G.Webb specializes in bulk haulage and has been using Continental Digital Solutions for many years now. “We’ve been a fan of the ContiConnect platform from the outset and use it as part of the Conti360° service package,” explains G.Webb’s Fleet Engineering Director, Paul Broker. “ContiConnect has enabled us to keep tabs on the current tire status of our trucks. It helps us to minimize fleet costs by giving us the information we need to stop a truck with a tire defect quickly and reliably before it escalates into a blowout or a breakdown.” ContiConnect has helped G.Webb to reduce the number of punctures and significantly improve work planning in the workshops. “With ContiConnect 2.0 and the multifunctional app – which offers fleet managers even greater operative flexibility – we are taking the next step towards predictive maintenance,” says Ralf Benack, Head of Fleet Solutions at Continental.
Better clarity and predictive maintenance
G.Webb has Continental’s tire pressure monitoring system fitted to the vast majority of its fleet. And all new vehicles are delivered with Continental iTires. iTires are tires which leave the factory with the sensor already integrated. Data from the tires on G.Webb’s short-distance trucks is recorded daily by the measuring station near the entrance to the site when they return. All the vehicles involved in long-distance jobs are connected to base via the ContiConnect platform. “The new ContiConnect 2.0 portal is even clearer, more user-friendly and simpler to interpret,” praises Broker. “And the data is more explicitly displayed. In a busy office, that really makes our work easier. We’re able to extract the vital information that we need quickly. If something is wrong with one of the tires, we pass this information through to the workshop immediately to begin repair preparations. ContiConnect 2.0 is a system upgrade that has a massively practical benefit to us,” he adds.
Improved compatibility optimizes working processes
G.Webb runs a fleet of 55 vehicles comprising trailers, semitrailers, and construction vehicles. The G.Webb engineering team has placed their trust in ContiConnect for many years, chiefly when it comes to optimizing maintenance efficiency. And the company particularly appreciates the enhanced mobile compatibility of ContiConnect 2.0. “The new ContiConnect 2.0 app has been a great addition and has helped us to refine how we do things,” reports Broker. “After a tire change at the roadside, the app enables us to recalibrate our tire sensors there and then. I.e. we don’t have to bring the vehicle into the workshop.” This saves time, optimizes processes, boosts the operational reliability of the vehicles and increases fleet efficiency. In addition, ContiConnect 2.0 improves overall fleet management: “I’ve also been able to grant access to our Conti360° Solutions account management team so that they can have live access to our fleet,” says Broker. “It’s certainly allowed us to be more widely connected and to react more quickly.”
Partnership based on trust underpins success and innovation
Ian Jackson from Continental Digital Solutions in England worked closely with Paul Broker to ensure the smooth migration over to the new ContiConnect 2.0 system. Now that successful testing of the platform is complete, the two companies are collaborating further on future ContiConnect additions. “It’s exciting to think that, in the not-too-distant future, the system will be able to provide more data about tread depths, remaining mileage and general rubber condition,” muses Broker.
And so an already excellent product will become even more appealing. “When it came to trialing ContiConnect 2.0, the Continental team dedicated lots of time to ensuring that the system was fully operational and that I was fully briefed on how to use it,” recalls Broker. “The Continental Digital Solutions package has transformed the way we work. There’s so much more predictability and efficiency in workshop loading. We rarely get blowouts now, when once it was a frequent occurrence. Certainly, we could not go back to a time without ContiConnect,” sums up G.Webb’s Fleet Engineering Director.
The ContiConnect 2.0 upgrade
The ContiConnect 2.0 new-generation tire management system was unveiled at the beginning of 2022. It builds upon existing functions and puts the framework in place for future platform developments to be integrated. Customer data is continuously analyzed within the cloud, with ‘big data’ and artificial intelligence helping to deliver precise forecasting and continue the drive towards predictive, rather than reactive maintenance. Users benefit from a new, multifunctional app that provides even greater operational flexibility for fleet engineers.
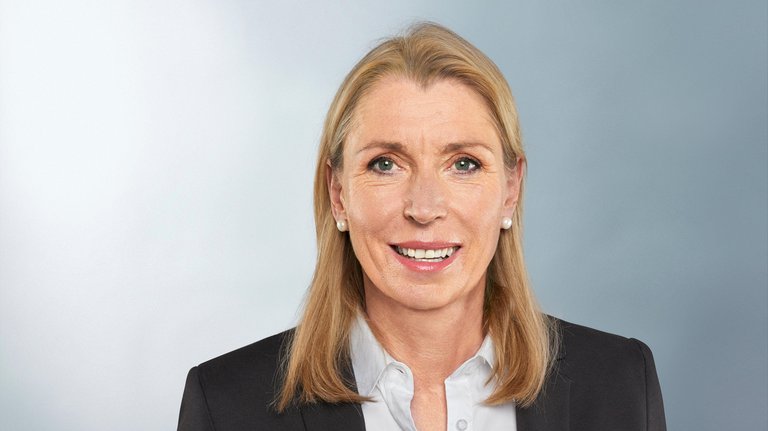
Annette Rojas
Spokesperson commercial vehicle tires
Public Relations, Media and Communication
Replacement Tires EMEA
Continental Reifen Deutschland GmbH