Continental To Test Tires in Dynamic Driving Simulator
- Simulator makes tire development in the original equipment business more efficient
- Professional test drivers will complete realistic driving scenarios virtually in the future
- Digital tire development leads to around 100,000 fewer test kilometers per year
- Dr. Boris Mergell, Head of Research and Development Tires business area: "The new simulator combines state-of-the-art technology with the vast experience of our professional test drivers.“
Hanover, Germany, April 7, 2021. Continental is investing in a state-of-the-art dynamic driving simulator in order to develop its premium tires for the original equipment business even more efficiently, sustainably, and precisely in line with customer requirements in the future. The high-tech installation from manufacturer Ansible Motion will go into operation in mid-2022 at Continental's largest European tire test center, the Contidrom in Wietze near Hanover. It is a Driver-in-the-loop simulator (DIL) that calculates exact driving dynamics parameters of the tires and those of the respective test vehicle. Thanks to its high mobility, the simulator can provide Continental's professional test drivers with subjective driving impressions, just like tire tests on the test track. Test drivers can experience new tire developments in the most diverse virtual test scenarios and driving situations.
"Developing and testing premium tires is a highly complex, time-intensive process. By using the new dynamic driving simulator, we will make this development process even more efficient in the future," says Dr. Boris Mergell, Head of Research and Development of the Tires business area. "We want to actively shape the virtual development process in the automotive industry in the tire sector as well. The new simulator combines state-of-the-art technology with the vast experience of our professional test drivers. Continental is one of the pioneers in the use of this innovative, hybrid test technology," he added.
Sustainable development: Around 100,000 test kilometers and 10,000 test tires saved
The new driving simulator brings significant benefits for tire development – and thus for Continental's customers. When decisive development steps and the associated test arrangements are shifted to the virtual world, this saves time, costs and valuable resources in the real world. The logistical effort of a wide variety of physical tests, for example, is significantly reduced because crucial parameters can be checked in the simulator. This is because the simulator is fed with the data of the particular vehicle model for which the new tire is being developed. This is supplemented by Continental's data on rubber compound, tire architecture and tread design.
Each test cycle completed in the driving simulator instead of on real roadways means fewer test tires that need to be built. The investment in the new test technology thus also contributes to Continental's extensive sustainability efforts. Among other things, the company's goal is to be the most progressive tire manufacturer in terms of environmental and socially responsible business practices by 2030. To achieve this, Continental is investing significantly in innovative technologies and processes along the entire value chain. The new driving simulator supports this with concrete figures from the real world: "If our test drivers sit in the simulator cockpit in the future and less at the wheel of a vehicle, around 100,000 kilometers less will be completed each year on real roads or test tracks," explains Dr. Holger Lange, Head of Passenger Tire Development for Continental's original equipment business. "We can also save around 10,000 test tires per year," he added. Until now, the final tuning of tires to real-life application scenarios always required the construction of a large number of test tires. The aim is to have to build significantly fewer such prototypes in the future thanks to the simulator.
Simulator offers versatile test possibilities
The test driver drives a very specific tire model for a specific model variant in the simulator. In the event of any anomalies, all parameters can be digitally adjusted at any time. This means that new tire models can be tested predictably in all conceivable areas of applications, driving situations and on a wide variety of surfaces, with reliable results at an early stage of the development process – and that for all vehicle and drive variants, for passenger cars as well as commercial vehicles, for electric, hybrid and combustion engine vehicles. Even new material variants – Continental is intensively researching the possible applications of sustainable materials for tire construction – can be extensively tested and further optimized before the first test tire has even been built.
Continental has selected Ansible Motion's Delta S3, the latest in simulation technology. With increased motion space of four-by-five meters, higher resolution and the ability to accurately evaluate tires in a virtual world, the Delta S3 will allow Continental's engineers to simulate accelerations over a longer period of time. This guarantees more realistic experiences, such as lane change vehicle maneuvers, tight and long-distance cornering, and driving on different surfaces.
Continental is a pioneer of innovative tire testing methods
Continental has long been one of the leading companies in the use of innovative tire testing technologies. The world's first automatic and weather-independent brake analysis system (AIBA; Automated Indoor Braking Analyzer) has been in operation at the Contidrom since 2012 – in close proximity, by the way, to the new driving simulator, which will also be used on the Contidrom site. In addition, since 2018, the company has been a pioneer in tire testing with autonomous test vehicles at its own test site in the US state of Texas.
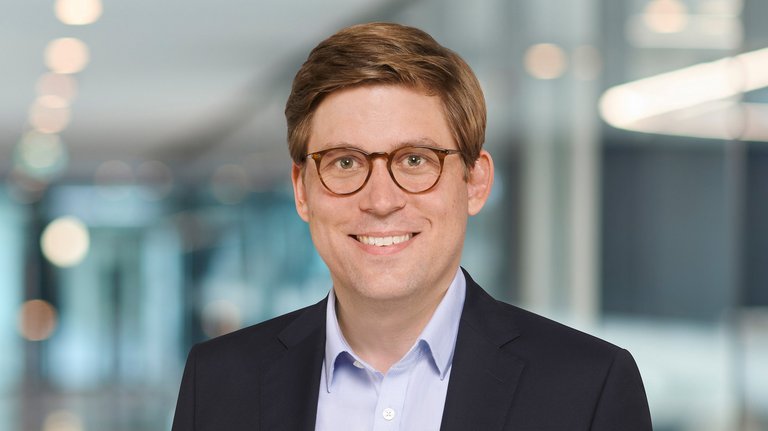
Henry Schniewind
Head of External Communications
Continental Tires