Continental’s Amata City Plant is First Company in Thailand to Receive “5S Best in Class” Certificate
- Technology company is a global leader in implementation of 5S
- 5S method is based on Kaizen approach and targets systematic improvement of workplace organization involving the entire workforce
- Outstanding result with 98 percent compliance despite relatively short implementation phase
Amata City (Thailand), Regensburg (Germany), January 29, 2018. Originating in Japan, the Kaizen philosophy of continuous improvement in a business context is becoming increasingly important in the automobile industry. One driving force in this context is the technology company Continental. At the end of 2014, the Continental site in Roding, Germany, became the first plant in the world in the automotive sector to receive a Kaizen “5S Best in Class” certificate for all of its departments. Then, early in 2017, Continental’s 28 Central Electronic Plants became the first worldwide factory network to gain 5S certification. Now the automotive supplier has again underlined its role as a Kaizen pioneer, with Continental’s Amata City plant recently becoming the first company in Thailand to be presented with the “5S Best in Class” certificate by the Kaizen Institute. At this plant with about 500 employees, the Continental Powertrain division’s Engine Systems business unit manufactures injector systems and high-pressure injection pumps for the Asian and European markets.
Based on the Kaizen approach, the 5S method targets the standardization and systematic improvement of workplace organization. With the involvement of the entire workforce, the aim is to create a working environment that ensures optimal quality and efficiency. “An uncompromising focus on quality, efficient, transparent processes and a high level of employee responsibility also form central pillars of the Continental Business System (CBS), the business philosophy of our company. So the 5S methodology makes a perfect match for our aspirations in terms of quality and efficiency,” says the head of the Engine Systems business unit, Wolfgang Breuer. “Amata City is an important site for us, particularly as the ASEAN region ranks among the automobile markets with the highest population density and shows great potential for growth. Our employees in Amata City can be proud of the fact that their factory is the first company in Thailand to be awarded a 5S certificate.”
Rapid learning, better quality control, optimized use of space
To send out a clear signal that the engagement of the entire workforce is essential to the certification process, Amata City kicked off the implementation of 5S by organizing a “Big Plant Cleaning Day”. Everyone spent half a day tidying up and clearing out every work area at the plant – from the Plant Manager’s office to the remotest corner of the warehouse. Then, early in May, the Kaizen Institute held an initial audit in line with the 5S criteria – and the plant emerged with 28 percent of the maximum score. For certification to take place, the minimum compliance level is 95 percent. What followed were trainings for every employee from manager to machine operator, as well as regular internal audits. The outcome was that, when the second audit by the Kaizen Institute took place a good three months later, the plant scored 90 percent. Just recently, Amata City completed its third audit with a score of 98 percent – an outstanding performance for first-time certification.
“Our plant’s motto is ‘Improvement never stops’. Through their impressive performance in achieving such an excellent result in such a short time, our employees have proven that this motto is truly lived at our plant. Because the fact is that the 5S method can only be applied successfully if the entire workforce is convinced it’s the right thing to do and actively drives it forward,” says Dr. Patrick Schmitt, General Manager of Continental’s Amata City plant. He goes on to provide examples of the progress that can be made through 5S. For example, the method can also be used to provide a clear overview of the quality indicators of each unit. This way, deviations from target values are immediately visible and the team in question can respond in a fast and targeted way. Another important aspect, according to Schmitt, is the elimination of unnecessary costs, for example by making more economical use of space. “In many areas we can reduce our space requirements considerably because workplace standardization in line with 5S means some things are no longer required.”
Certificate presented by “Mr. Kaizen” in person
“Attaining such an outstanding result in such a short time is a huge achievement for a plant of this size,” says Masaaki Imai in praise of the Continental plant. Imai, also known as “Mr. Kaizen” founded the Kaizen Institute back in 1985. Today the organization supports various branches of industry in more than 50 countries. At the 2018 KAIZEN™ Conference in Kuala Lumpur, Imai himself personally presented the 5S certificate to Amata City General Manager Patrick Schmitt who had also been invited to address the KAIZEN™ Conference. “The challenge now,” says Imai, “is to continue to apply the 5S process systematically and thereby assure continuous improvements going forward.” To demonstrate this systematic application, each company certified to 5S must “defend” its certificate once a year in the course of an audit and attain a compliance level of at least 95 percent.
The term “kaizen” is made up of the two Japanese words kai (change) and zen (for the better). The abbreviation 5S stands for the five steps called Seiri (Sort), Seiton (Straighten), Seiso (Shine), Seiketsu (Standardize) and Shitsuke (Sustain).
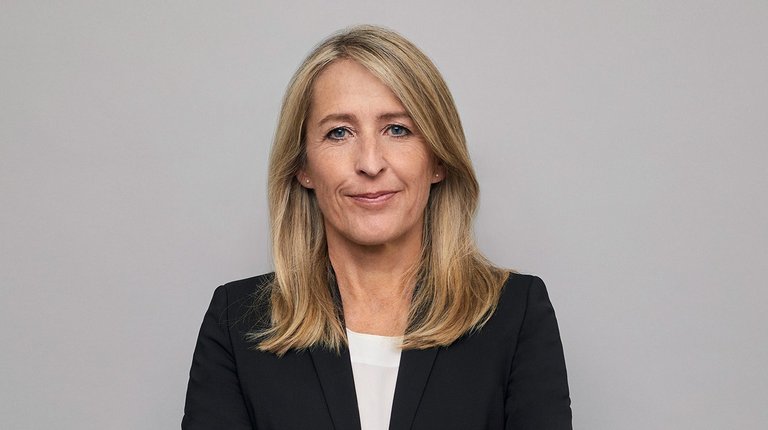
Simone Geldhäuser
Head of Media Relations, Spokesperson Finance, Business and Technology
Vitesco Technologies