From Diesel to Hybrid: New Continental Control Unit is Control Center in All Mercedes E-Class
- Newly developed central powertrain controller acts as a gateway and controls communication between all the powertrain's control units, and can also take on the control functions of other devices
- The controller is based on the new Continental EMS3 platform, whose architecture has already been fully designed with the complex requirements in mind of electrified and interconnected drives
- Usage in all models of the new E-Class, including plug-in hybrid version
Regensburg, March 28, 2017. Whether it's a gasoline vehicle, diesel vehicle, or a plug-in hybrid: in all models of the new Mercedes E-Class, the central powertrain controller (CPC) from Continental acts as a gateway in taking on the role of the drive's electronic control center. This completely newly developed control unit features a powerful multicore processor and an open variable interconnection architecture based on the new Continental engine control unit platform, Engine Management System 3 (EMS3). It is in charge of all communication between the powertrain's various control units – and it can also assume the control functions of other devices.
“The central powertrain controller is the first control unit based on our newly developed EMS3 platform. It has been custom-made to meet the future requirements of electrified and interconnected powertrains. We are glad that Mercedes was so impressed with this new technology that they incorporated it into the new E-Class. I would like to express my sincere gratitude for this show of trust and the good cooperation,” says Wolfgang Breuer, Head of the Engine Systems Business Unit at the Continental Powertrain Division.
Real-time communication and new distribution of powertrain functions
The launch of the CPC is connected with new powertrain interconnectivity. To perform its function as a communication center for the individual control units in real time, the CPC works with the most powerful microcontrollers currently available. The hardware is based on the new generation Continental engine control unit which, for the first time, uses a multicore architecture with three computer cores inclusive monitoring core. This ensures that the high safety requirements of ISO 26262 can be met. The control unit is equipped with up to 5 CAN channels, a flexray channel, up to 2 LIN channels, various digital and analog inputs and outputs and up to 2 SENT interfaces. The use of the Continental-specific electronics components makes possible a very compact design.
Thanks to its powerful multicore architecture, the CPC can also take on further functions in addition to its role as a gateway. “This gives the automotive manufacturer completely new opportunities in distributing powertrain functions over several control units,” says Breuer.
EMS3: Pioneering Continental platform with holistic approach
The CPC software is based on the new EMS3 platform. In addition to the multicore support, one of the most important features of the EMS3 system architecture is its compatibility with the industry standard AUTOSAR 4. This open software architecture simplifies the integration of external software; in many cases existing subsystems can continue to be used seamlessly. With its usage spectrum from gasoline and diesel vehicles right up to hybrid vehicles, EMS3 adopts a holistic approach with which the number of variants and complexity in the entire system is reduced in the long term.
The pioneering Continental platform has been fully designed with future requirements in mind. In electrified drives, EMS3 allows the integration of new, efficiency-enhancing functions such as the forecast-based “connected Energy Management” (cEM), which works with cloud-based data. This data is delivered, for example, by the Continental system eHorizon (electronic horizon), which creates a three-dimensional profile of the route. The control unit then identifies in advance the sections of the route where energy can be gained and how this energy can be used most profitably. For example, it can inform the driver of upcoming stoppages in good time in order to ensure optimum regeneration.
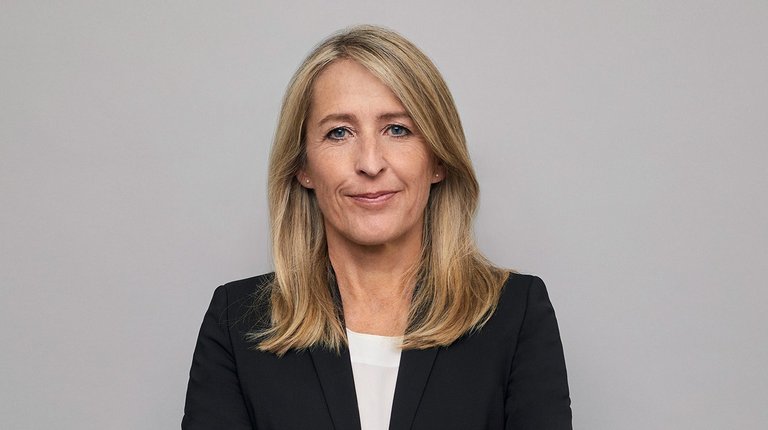
Simone Geldhäuser
Head of Media Relations, Spokesperson Finance, Business and Technology
Vitesco Technologies