More Compact, more Efficient, more Cost-Effective: Close Coupled Catalyst for Heavy Commercial Vehicles
- Close coupled positioning of the diesel oxidation catalytic converter makes exhaust gas aftertreatment more efficient and cost-effective
- Re-locating the exhaust gas aftertreatment system creates about 30% more space and allows the tank size to be increased
- The new catalyst substrate enables optimum use of installation space with less weight
Regensburg, Lohmar, Hanover, August 25, 2016. At the 66th IAA Commercial Vehicles in Hanover (September 22–29), the international technology company Continental will present a solution for close coupled exhaust gas aftertreatment systems in heavy commercial vehicles. Positioning the diesel oxidation catalytic converter (DOC) near the engine means that the volume of the DOC can be reduced by around 30%. At the same time, using the recently developed catalyst substrate featuring the CS-Design® (Crossversal Structure – see details below) can additionally decrease the weight of the DOC by 20%. The low level of heat loss and the high degree of conversion efficiency of the innovative CS cell structure will help to meet future nitrogen oxide emission limits such as those set out in the CARB 2023 (California Air Resources Board) regulation in the U.S.A. Thanks to the higher working temperature in the DOC, the subsequent injection of the urea solution can begin earlier. In addition to the DOC, the solution to be presented in Hanover also includes the urea dosing system integrated in the tank, the SCR (Selective Catalytic Reduction) control unit, and the metallic catalyst substrate for complete evaporation of the urea solution.
“Until now, positioning the DOC in close coupled position to the engine in heavy commercial vehicles was impossible due to the installation space available,” says Dr. Markus Distelhoff, Head of the Fuel & Exhaust Management Business Unit of the Continental Powertrain Division. “Incorporating a particularly lightweight and efficient catalyst substrate, our solution now makes it possible to achieve compact, square geometries that can be positioned close to the engine, thereby opening up a number of advantages.”
Thanks to the reduced material used in the DOC, the new close coupled catalytic converter solution with at least the same high level of overall system efficiency, is more cost-effective than previous exhaust gas aftertreatment solutions, which were fitted to the chassis between the axles. The decreased volume requirement at this point can benefit the tank volume.
Adapting the Diesel Oxidation Catalytic Converter to the Space Available
The engine of heavy commercial vehicles is designed for lowest fuel efficiency at high loads. However, in other operating situations, engines hardly release any heat. Although this benefits the fuel efficiency level it presents a challenge to exhaust gas aftertreatment systems. If the exhaust gas is already at a low temperature at the engine, a long pipe section between the engine and the exhaust gas aftertreatment system, fitted to the chassis between the wheels, is even more disadvantageous as the exhaust gas continues to cool. Particularly in inner-city traffic, it can be difficult to ensure an adequate conversion temperature. Installing the DOC close to the engine changes this. With this set-up, heat loss through the flow path can be disregarded. As the efficiency of the DOC increases with the operating temperature, the volume of the DOC can be reduced. As such, when Continental carried out a test with the DOC near the engine, it was able to reduce the volume of the DOC by 30% from 11.3 to 7.8 liters.
Continental uses the new CS catalyst substrate in its solution, where the DOC is installed near the engine. With this corrugated foil material, the waved structure exhibits a slight slant angle (hence the name Crossversal Structure, “CS”). By combining alternating left and right diagonal waves, the DOC structure manages without an intermediate foil for the first time. As a result, the amount of materials used and the weight decrease by 20%. At the same time, the efficiency of the NOx converter increases as the diagonal course of the waves generates turbulence, which brings nitrogen oxide in exhaust gas in better contact with the catalytic-coated surface of the substrate.
Positive Effects of Installation near the Engine
In diesel passenger cars, installing the DOC near the engine is now routine. This trend cannot be implemented so quickly for heavy commercial vehicles in particular, as the underlying chassis has a very long service life. It is for this reason that the first step towards installation close to the engine can only take place using particularly compact catalytic converters.
Successfully installing the DOC close to the engine results in additional benefits according to Rolf Brück, Head of Catalysts Product Line, Fuel & Exhaust Management: “For example, the higher temperature level enables earlier release for the injection of the urea solution downstream of the DOC. As a result, NOx conversion starts earlier.” The higher temperature in conjunction with the structured metallic foil materials, on which the urea solution is sprayed, results in the complete evaporation of the urea solution. This prevents the build-up of deposits downstream. These deposits would restrict cross sections, impair the control quality of the exhaust gas aftertreatment system and destroy gas-conveying components such as flexible elements.
With the long-term and likely complete re-location of the exhaust gas aftertreatment system towards the engine, the volume requirement for parts fitted to the chassis decreases, freeing up space for an increased fuel tank volume. “Installing the exhaust gas aftertreatment system near the engine is a prerequisite. If you don’t start at the front then you won’t have the benefits at the back,” Brück adds.
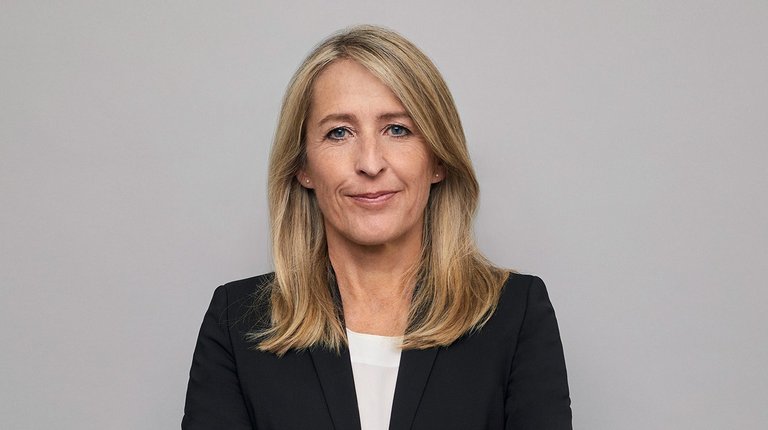
Simone Geldhäuser
Head of Media Relations, Spokesperson Finance, Business and Technology
Vitesco Technologies