No Chance for Hackers: Secure Sensor Technology for Continental Hoses and Lines
- The sensIC project demonstrates integrated sensor technology based on printed electronics in hoses and lines for battery electric vehicles (BEV)
- Continental expands its portfolio with hybrid electronics combining printed electronics and silicon chips
- Project partnership with industrial firms and universities to run until spring 2024
- Enhanced safety in vehicles and sensitive production facilities thanks to a sensor system involving a silicon chip for temperature measurement, a non-clonable safety feature, and external tamper protection by means of particle-based fluorescence detection
Hanover, Germany, April 22, 2021. For some time now, the technology company Continental has been equipping many of its rubber and plastic products with sensor technology, e.g. for condition monitoring, efficiency control and process regulation. With the goal of more comprehensively equipping its rubber and elastomer solutions with sensor technology and intelligent systems, Continental has launched a collaboration – the sensIC project – with partners from industry and R&D. As the collaborative coordinator, Continental is driving the project forward with its integrated sensor technology based on printed electronics for hoses and lines installed in electric vehicles.
Media-carrying lines for thermal management in electric vehicles
The project, which is being co-funded by the German Federal Ministry of Education and Research to the tune of 2.9 million euros, involves installing hoses for thermal management in electric vehicles with integrated temperature sensors. The electronics are designed so as to rule out manipulation during production, at subsequent stages of the supply chain or during actual use. Given the trend towards integrated electronics in automobiles and systems, achieving a high degree of safety is becoming more and more critical. This trend is also paving the way for extended functionality and – to a greater extent than ever before – making it possible to offer services and digital business models spanning the entire service life of products, e.g. live information on system health, predictive maintenance services or post-delivery functional upgrades.
“The sensIC project exemplifies how integrated sensor technology based on printed electronics can be realized on an industrial scale. This represents a major contribution to the mobility revolution and enabling increasingly energy-efficient and sustainable solutions,” says Dr. Tim Wolfer who – in his role as project manager for functional printing processes – is overseeing the R&D initiative. Continental’s declared goal for the project is to expand its product portfolio with safe electronics by integrating temperature sensor technology and communication modules into tubing systems. The resulting hybrid systems are based on a combination of printed electronics and specially manufactured silicon chips. The project is slated for completion in the spring of 2024.
Secure sensor technology guards against cyberattacks on vehicles and plants
Meanwhile, Continental is also equipping hoses in industrial facilities with sensors to monitor operating status and immediately detect any faulty or malicious manipulation of processes, for example in pharmaceutical or food processing plants. Another high-risk scenario being addressed: cyberattacks on vehicles, for sensors gauging and streaming such physical data as pressure or temperature are particularly vulnerable to hacking attempts. The security of sensors and sensor data is therefore of critical importance.
“In order to meet precisely such requirements, it is important that we equip our products with a combination of mechanically flexible electrical circuitry and less flexible sensor chips so as to add value while increasing safety without added effort, and with the lowest possible added cost,” emphasizes Wolfer. As an outcome of the sensIC project (whose acronym is made up of “sens” for sensor and “IC” for integrated circuit), hybrid integrated sensor circuits will be added to hoses and lines used in automotive and industrial applications for the monitoring of parameters such as battery temperature, or in drinking water systems and in the context of pharmaceuticals. This intelligent and safe sensor technology will be deployed in the form of a silicon chip for temperature measurement, a PUF (physical unclonable function) and external tamper protection by means of particle-based fluorescence detection.
More safety thanks to hybrid PUF circuitry
And this is how it works in detail: As an electronic, non-clonable identifier, a differential PUF circuit based on printed transistors and silicon-based read-in and read-out electronics is integrated with a sensor circuit. The sensor circuit contains a silicon IC that communicates with the hybrid PUF via a corresponding interface made possible by a specially engineered, packaging technology, thus forming a “secure” overall system.
Integration is achieved by bonding the PUF to the silicon IC by additive processes, followed by encapsulation of the entire system. In addition to this, the security of the overall component will be enhanced by means of a tamper-proof, unambiguous recognition feature made possible by a random pattern of special inorganic fluorescent particles blended into suitable material components with a sealing effect.
In the final phase of the project, the integrated system will be subjected to the usual mechanical stress tests using a technology demonstrator, and then its electronic system will have to prove it can ward off various model-based simulations of cyberattacks.
A system suitable for many different applications
Besides its target use in the context of secure battery sensors, the resulting system can also be used in a wide variety of other applications. Among the possible uses to be explored by the project’s partners is the monitoring of safety-critical hoses and lines for pharmaceuticals and raw materials, the goal being to ensure that they are completely tamper-proof, and that all components used can be tracked throughout their entire service lives.
Teaming up with Continental on this project are: Cyient GmbH, Polysecure GmbH, the Karlsruhe Institute of Technology (KIT), the Leibniz Institute for New Materials, Offenburg University of Applied Sciences and Elmos Semiconductor SE.
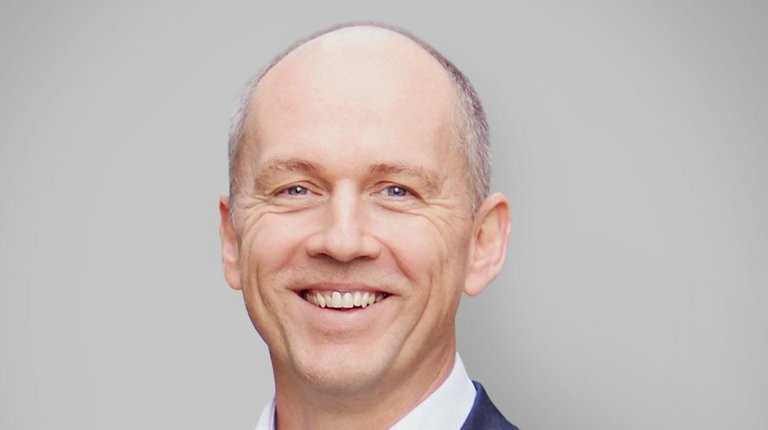
Wolfgang Reinert
Head of Media & Public Relations
ContiTech
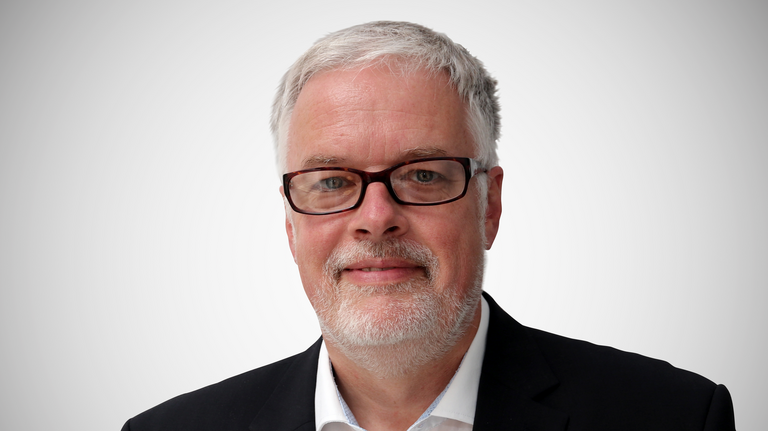
Axel Schmidt
Head of Communications
ContiTech Surface Solutions