Never underestimate the power of collaboration and TEAM work
During 2018, one of the Compound Development projects for industrial hoses undertaken at our location Grimsby, UK, was to improve the adhesion between a friction compound and one of the main reinforcing cord fabrics. At that time, the project did not provide significant improvements, but I took it as a personal challenge to investigate further the technology behind rubber to textile adhesion with the aim of finding and developing new options which had not been considered in the plant before. The result of this determined effort was successful production trials – the first in business area ContiTech – of a cord fabric using the COKOON sustainable textile dipping system.
Having reviewed the extensive development history in Grimsby, I became more interested in the possibilities with the textile dipping technology, not just compounds alone. Following initial contacts with textile experts in R&D, we agreed that both rubber compound and textile dip should be developed together to achieve the optimum rubber to textile adhesion. I was motivated to search for in-house support for dip and textile development opportunities within Continental, which lead to contact with reinforcements colleagues at the business area R&D and the start of the collaborative project which would result in the first ContiTech production trial of a cord fabric dipped with the COKOON textile adhesion system.
ContiTech central R&D reinforcements provided significant knowledge of the textile manufacturing and dipping possibilities which exist within Continental and recommended that material experts and textile developers in Lousado, Portugal, who had never worked with Grimsby before, were approached to start a collaboration project. The team Portugal were contacted, and technical details of Grimsby textiles were shared, along with the development aims. The team in Portugal started to develop in-house versions of the fabrics and provided laboratory versions of the textiles, of which two were found to have promising properties. Following further discussions, it was revealed that one of the two dip systems that showed good adhesion to the Grimsby friction compound was based on the COKOON technology – a sustainable and Resorcinol Formaldehyde (RF)-free dipping system jointly developed by Continental and Kordsa. Following successful laboratory results, a production roll of the COKOON dipped fabric was purchased from Continental in Portugal to verify the suitability of the material in the Grimsby process. In early 2020, a production roll was received and evaluated in the Grimsby laboratory, where it was found to fully comply to the purchase specification requirements. The fabric roll was subsequently processed and evaluated side by side against standard production materials with very positive feedback and comparable test results. This trial at Grimsby is the first in the business area ContiTech to evaluate a COKOON dipped cord fabric on a production scale. Invaluable support from ContiTech central R&D, our team in Portugal and internal departments of Grimsby was key to the success of the project.
The bottom line is that if someone wants to step outside of their comfort zone (Passion to Win) and use internal collaboration possibilities for growth (For One Another) and for future product developments, Continental is an organisation that supports the individual as well as the team (Trust and Freedom to Act).
This article was written by our employee.
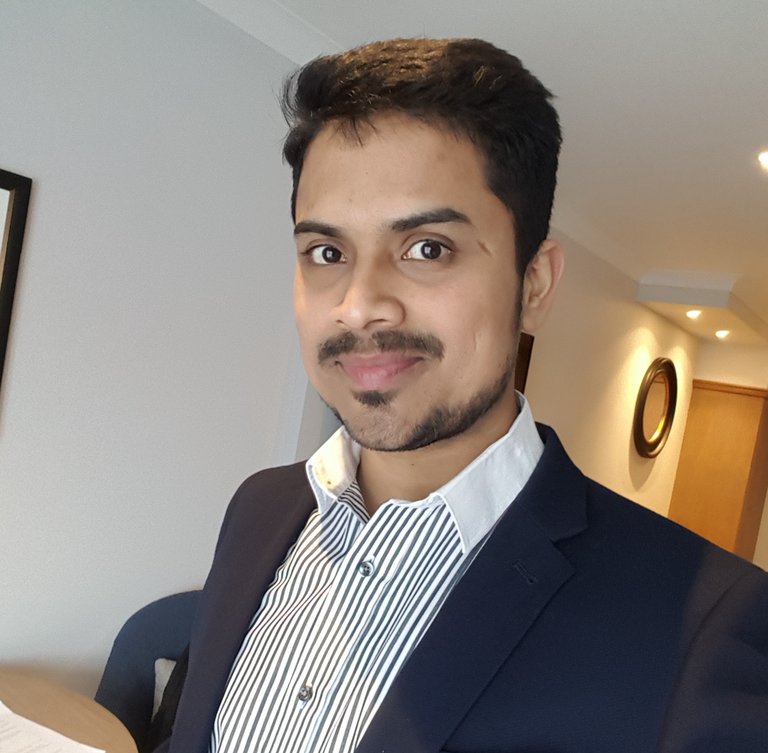