Health and Safety Measures to Prevent Spread of Coronavirus at Continental
Note: This article contains data from April 2nd and might not be 100% current when you read this.
Hello everybody, my name is Christian Feldhaus, I am head of Group Safety & Health at Continental. Together with my global team, I oversee the welfare and health protection of Continental employees worldwide every day, but especially during the Corona crisis.
Of course, the coronavirus poses enormous challenges for us. However, we are thankful that with over 240,000 employees worldwide, the number of infected employees at Continental remains in the double digits and with most on their way to recovery or mild symptoms. On another positive note, those who have tested positive for the virus contracted it primarily in their free time and not at work. This is a result of our early cooperation with the health authorities and numerous protective measures.
Our top priority and the basis of our approach is the health and safety of all employees. It comes first, followed by the maintenance of operations. As a Group Crisis Team, we are closely monitoring the situation by consulting the specialist Media constantly. We are in close contact to the crisis teams of the affected countries as well as other global companies. A continuous risk assessment is being conducted by numerous factors like the number of confirmed cases per population, density of population, quality of the medical system, rules by national government or international organizations like the World Health Organization. With our crisis teams on global, national and local level we are going to great lengths to protect our employees. Wherever feasible, we are asking colleagues to work from home in order to minimize personal contact and to increase safety for those who are at the workplace. Of course, not all employees can work from home. For this reason, we took numerous measures at our plants at a very early stage to prevent the spread and transmission of the virus to the greatest extent possible.
So, what exactly are we doing on-site? We have substantially increased the frequency of cleaning at all locations. Shared rooms such as showers and smoking cubicles are being cleaned very often, as are handrails and door handles. We are informing and training staff, for example about how they can significantly reduce the risk of infection through simple measures such as washing their hands or correctly receiving goods. Wherever necessary, we have issued millions of masks, sanitizers, gloves and other personnel protection equipment in recent weeks. Protective equipment alone won’t stop the spread, so we also re-organized the shift models in order to minimize personal contact and eliminated all face-to-face shift handovers at the plants. We are reducing or staggering shifts for the same reason. In the canteens, staff are requested to eat in shifts and distance themselves from one another. In addition, there is no longer any self-service. In some cases, only packed lunches are provided to minimize the risk of infection. We have assigned teams for business-critical production processes, so that if one team member falls ill, another team member can take over. Another very specific example, we have decommissioned time clocks as a source of potential transmission of the virus. All of these measures are based on scientific knowledge and valuable input from countries that already have extensive experience in dealing with the corona crisis.
As a physician, it is particularly important to me that employees who are more vulnerable, such as those with pre-existing illnesses or pregnant women, can be given sick leave or time off on the basis of a case-by-case screening with the company doctor. Our efforts are also aimed at ensuring that employees returning from risk areas place themselves in self-quarantine for 14 days so as not to endanger others.
When Continental begins ramping up the production at its plants again on a broad scale, we will continue to implement the extensive measures previously mentioned. In addition, no location will resume operations without having first carried out a targeted risk analysis for its entire production process in line with established occupational safety guidelines. The focus here will be on preventing any form of disease transmission. We are not accepting, and we will not accept that it is more risky to go to work than to go for a walk.
It’s great to see how our global and local teams collaborate and work together without stopping at any hierarchical or geographical border. This is really living our value For One Another and I can only use this opportunity to give a big applause to the teams already now for their great work.
This article was written by our employee.
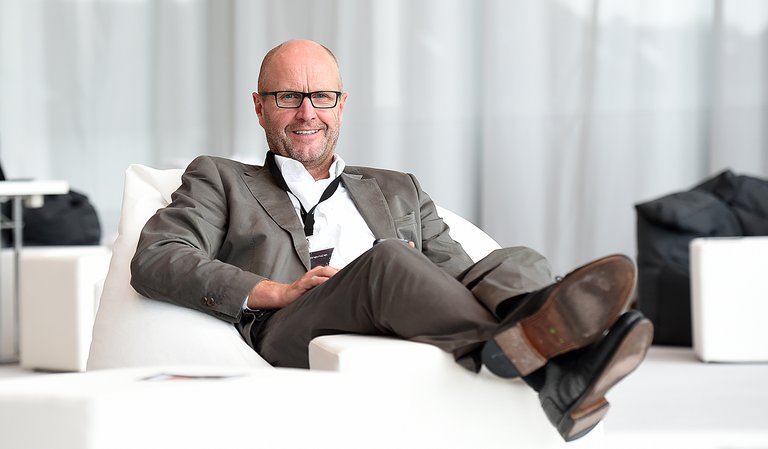
Prof. Dr. Christian Feldhaus