Continental liefert weltweit ersten Turbolader mit Aluminium-Turbinengehäuse für Pkw Serieneinsatz
- Meilenstein: Continental Turbolader mit wassergekühltem Aluminium -Turbinengehäuse ist im 3-Zylinder-Ottomotor des MINI in Serie gegangen
- Weltweit kommt damit erstmals ein Turbolader dieser Art in einem Pkw zum Einsatz
- Wasserkühlung ermöglicht den Einsatz des Leichtbauwerkstoffs und damit eine deutliche Gewichtsersparnis von nahezu 30% bei gleichzeitigen Kosten- und Systemvorteilen
Regensburg, den 15. Juli 2014. Kleinerer Hubraum und geringer Kraftstoffverbrauch bei gleicher oder sogar gesteigerter Leistung – das ist die Erfolgsformel beim Downsizing. Damit dies realisiert werden kann, ist ein modernes Aufladesystem erforderlich. Dieser weltweite Entwicklungstrend zur Turboaufladung bei Ottomotoren ist in vollem Gange. Der internationale Automobilzulieferer Continental unterstützt diesen Trend und setzt mit seiner wegweisenden und innovativen Turboladertechnologie Meilensteine. Der erste Continental-Turbolader ging bereits 2011 in einem hoch effizienten und mehrfach preisgekrönten 1,0 l Motor in Serie. Dieser Erfolgsgeschichte fügt das Unternehmen nun mit einer technologischen Weltpremiere ein weiteres Kapitel hinzu: Die Powertrain Entwickler von Continental haben den ersten Pkw-Turbolader mit einem Turbinengehäuse aus Aluminium in Serie gebracht. Das Aggregat wird seit dem Frühjahr 2014 in die 3-Zylinder-Ottomotoren für den MINI Hatch integriert. „Aluminium im Pkw-Turboladerbau ist ein Meilenstein“, sagt Wolfgang Breuer, Leiter der Business Unit Engine Systems, Division Powertrain. „Mit diesem Leichtbauwerkstoff sparen wir fast 30% Gewicht gegenüber einem herkömmlichen Stahlturbolader, senken dabei die Kosten und erschließen Systemvorteile.“
Seine Premiere hat der innovative Turbolader von Continental mit Aluminium-Turbinengehäuse in einer anspruchsvollen Downsizing-Anwendung: einem aufgeladenen
3-Zylindermotor mit 1,5 l Hubraum und 100 kW Leistung. „Der Turbolader ist aber nicht nur wegen des Aluminiums eine Besonderheit. Er ist auch keine typische Anbaukomponente mehr, sondern integraler Bestandteil des Motors“, erläutert Udo Schwerdel, Leiter der Produktlinie Turbolader, Engine Systems, Division Powertrain. „Um die Anforderungen an das Aggregat und seine Einbindung in den Zylinderkopf zu erfüllen, haben wir schon in der Simulationsphase eng mit der BMW Group zusammengearbeitet, ein Vertrauensbeweis, den wir außerordentlich hoch schätzen.“
Aluminium im Turbolader: Weniger Gewicht, weniger Kraftstoffverbrauch
Während herkömmliche Turboladerkonstruktionen mit Stahlgehäuse bei Volllastbetrieb durchaus rot glühen können, bewahrt das Turbinengehäuse aus Aluminium einen kühlen Kopf. „Das doppelwandige Aluminium-Turbinengehäuse umgibt den heißesten Bereich mit einem kühlenden Wassermantel“, sagt Schwerdel. Dank des Kühlmittelstroms, der diesen Mantel durchfließt, wird die Oberfläche des Gehäuses außen nicht heißer als 120 °C, innen bleibt die Temperatur unter 350 °C. Das hat laut Udo Schwerdel gleich zwei Vorteile: „Erstens ist viel weniger Aufwand zum Wärmeschutz benachbarter Komponenten nötig. Zweitens bewirkt die Kühlung des Abgasstroms, dass der Katalysator thermisch nicht so hoch belastet wird und daher kaum altert.“ Gleichzeitig sorgt ein elektrischer Aktuator am Waste-Gate mit seiner Dynamik dafür, dass sich der Katalysator schnell aufheizt.
Basierend auf dem vorgegebenen Baukastenprinzip ist der Turbolader zwar eng in den Motor integriert (er ist beispielsweise fester Bestandteil des Abgaskrümmers), aber über die Schnittstelle am Zylinderkopf lassen sich auch Continental-Turbolader mit Stahlgehäuse an denselben Grundmotor anbinden. Der Fahrzeughersteller nutzt diese Option für Hochleistungsmotoren sowie für Exportfahrzeuge, die in heiße Länder gehen. Bei den Stahlausführungen wird das Lagergehäuse im Inneren des Turboladers gekühlt, beim Aluminium-Turbolader genügt die Kühlung von außen.
Pro Aluminium-Turbolader werden im MINI 1,2 kg Gewicht eingespart. Da weniger Gewicht auch weniger Kraftstoffverbrauch bedeutet, unterstützt der Leichtbauwerkstoff die anspruchsvollen Verbrauchs- und Emissionsziele der Automobilindustrie. Und trotz des Mehraufwands für die Wasserkühlung sind diese Turbolader insgesamt günstiger für den Automobilhersteller. „Bei Stahlgehäusen treiben hochwarmfeste Werkstoffe wie Nickelbasislegierungen die Preise“, so Schwerdel, „unsere Aluminium-Legierung dagegen ist ein wirtschaftlicher Werkstoff.“
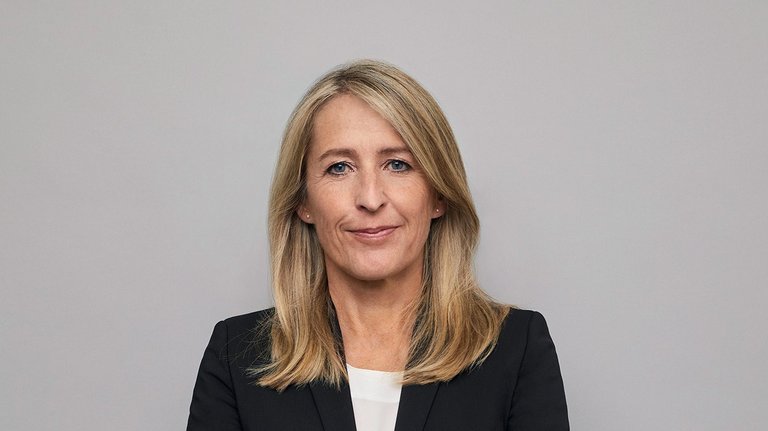
Simone Geldhäuser
Leiterin Medien
Vitesco Technologies